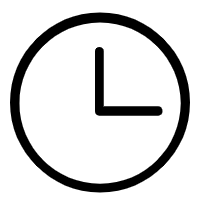
In the field of modern Machining, the Horizontal Machining Center (HMC) is widely used in the mass production of complex parts because of its high efficiency, high precision and flexibility. However, in high-intensity continuous machining, an effective chip removal system is one of the key factors to ensure processing quality and equipment stability. Poor chip removal will not only affect the quality of the machining surface, but also may cause equipment failure and even safety accidents. Therefore, it is particularly important to analyze the causes of chip removal in horizontal machining center.
Chip removal system design defect
First of all, the chip removal problem may arise from the inadequate design of the chip removal system of the equipment itself. This includes that the chute size is too small to quickly remove a large number of cutting debris; The location of chip discharge port is not reasonable, resulting in chip accumulation around the tool or workpiece; Or the chip removal device is not powered enough to remove long or tangled chips from the processing area in a timely manner.
Improper cutting parameters
Secondly, unreasonable cutting parameter Settings are also a common cause of poor chip removal. When cutting at high speed, if the feed speed is too high, the chips become fine and easy to wrap; The low speed and large feed may lead to the formation of large chips, both of which may increase the difficulty of chip removal. At the same time, the choice of cutting depth and cutting width also need to be careful, too large cutting amount will produce a large number of chips, which poses a challenge to the chip removal system.
Tool selection and wear
The type, geometry and wear state of the tool have direct influence on the chip removal effect. For example, the use of improper tip corners or edge angles may cause chips to curl and not easily discharge. In addition, worn tools can reduce cutting efficiency, produce more fine or irregular chips, and aggravate chip removal difficulties.
Workpiece material characteristics
The chip characteristics of workpiece with different materials during processing are significantly different. High hardness materials (such as stainless steel, titanium alloy) tend to produce long filaments or ductile chips, which are more difficult to effectively remove. The heat treatment state of the material also affects the chip removal performance during the cutting process.
Improper use of coolant
The choice of coolant is as important to chip removal as the application. The right amount and correct coolant can not only effectively cool the temperature, reduce tool wear, but also help the chip discharge smoothly. However, if the coolant pressure is insufficient, the flow rate is improper or the viscosity of the selected coolant is too high, it may hinder the flow of chips and cause blockage.
Maintenance and cleaning are not timely
Finally, the neglect of routine maintenance is also a factor that cannot be ignored. Regular cleaning of the chip extractor, filter and inside the machine tool to prevent chip accumulation and clogging the system is the basis for maintaining good chip removal performance.
In summary, the root causes of chip removal problems in horizontal machining centers are diverse, involving design, operation, maintenance and other levels. By comprehensively analyzing the above factors and taking corresponding optimization measures, the processing efficiency and safety can be significantly improved to ensure the smooth progress of the processing.