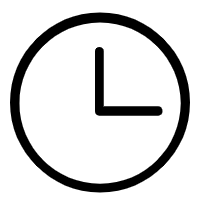
The speed of CNC vertical lathe has an important impact on the machining process. The choice of rotation speed directly affects many aspects such as cutting speed, cutting force, machined surface quality, tool life, etc. The following is the impact of CNC vertical lathe speed on processing:
1. Cutting speed: The CNC vertical lathe speed determines the linear speed of the tool during processing, which is the cutting speed. The appropriate cutting speed of CNC vertical lathe can ensure the stability and efficiency of the cutting process, while avoiding too high or too low cutting speed, which will cause excessive tool wear or low processing efficiency.
2. Cutting force: The CNC vertical lathe speed directly affects the cutting force. Generally speaking, increasing the rotational speed can reduce the unit cutting force, thereby reducing the load on the machine tool and tool during the cutting process, helping to improve machining accuracy and extend tool life.
3. Processing surface quality: The appropriate speed of the CNC vertical lathe can improve the smoothness and precision of the processing surface. Too high a rotational speed may lead to excessively high cutting temperatures, affecting the quality of the machined surface; while too low a rotational speed may result in insufficient cutting and increased surface roughness.
4. Tool life: The appropriate speed of CNC vertical lathe can extend the service life of the tool. Too high a rotational speed can easily lead to increased tool wear, while too low a rotational speed may cause the tool to be subjected to excessive force loads during machining, accelerating wear.
5. Processing efficiency: Appropriate selection of speed for CNC vertical lathe can improve processing efficiency. On the premise of ensuring the processing quality, the CNC vertical lathe can increase the cutting speed by reasonably increasing the rotation speed, thereby shortening the processing cycle and improving production efficiency.
Therefore, the selection of CNC vertical lathe speed needs to comprehensively consider factors such as workpiece material, tool type, processing requirements, etc., and adjust it according to the specific situation to achieve the best processing effect.