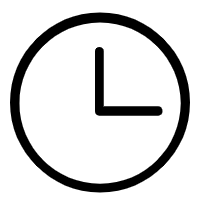
There are many factors that affect the cutting efficiency of turn-milling composite machine tools, including the performance of the machine tool itself, cutting tools, workpiece materials, and cutting parameters. Here are some of the main factors:
1. CNC system performance: The performance of the CNC system is directly related to the movement accuracy and response speed of the machine tool. High-performance CNC systems can improve the cutting accuracy and efficiency of turn-milling machine tools.
2. Spindle speed and power: The choice of spindle speed and power affects the cutting speed and cutting ability. Appropriate spindle parameters can improve cutting efficiency while ensuring that the tool is not prone to wear.
3. Tool selection: Suitable cutting tools are crucial to cutting efficiency. Choosing the right tool type, tool material, and tool coating can increase cutting speeds, extend tool life, and reduce thermal deformation during cutting.
4. Workpiece material: Different materials have different cutting properties, so the choice of workpiece material will affect the cutting efficiency of the turning-milling composite machine tool. Factors such as hardness and machinability need to be carefully considered before machining.
5. Cutting speed, feed speed and cutting depth: These cutting parameters directly affect cutting efficiency. A reasonable combination of cutting speed, feed speed and cutting depth can improve processing efficiency while ensuring the life of the tool and workpiece.
6. Cooling and lubrication: Using appropriate cooling and lubrication systems can reduce cutting temperature and tool wear, thereby improving the cutting efficiency of turn-milling composite machine tools.
7. Process planning and program optimization: Reasonable process planning and optimized processing programs can reduce unnecessary cutting time and improve processing efficiency.
8. Clamping method and tool switching time: The way the workpiece is clamped and the tool changing time will have an impact on cutting efficiency. Fast and stable clamping systems and quick tool changes reduce non-productive time.
Considering and optimizing these factors can effectively improve the cutting efficiency of turn-milling composite machine tools, reduce production costs, and improve processing quality.