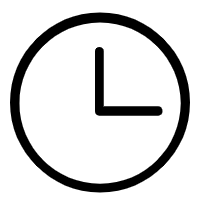
The workpiece clamping of CNC vertical lathe can usually adopt the following methods:
1. Three-jaw chuck clamping: This is a common clamping method, using a three-jaw chuck to fix the workpiece. The jaws of the chuck hold the workpiece by adjusting and clamping the nut. During the specific operation, the workpiece is placed in the chuck, and the contact between the workpiece and the chuck is ensured evenly. After the position is determined, the chuck nut is rotated to clamp the workpiece.
2. Four-jaw chuck clamping: Similar to the three-jaw chuck, the four-jaw chuck has better workpiece clamping uniformity and stability. The four-jaw chuck can adjust the position of the jaws according to the shape of the workpiece to ensure better clamping effect.
3. Pneumatic/hydraulic chuck clamping: a device that uses a pneumatic or hydraulic system to clamp a workpiece. This clamping method is suitable for large or heavy workpieces with high clamping force and stability.
4. Clamping with slider and threaded rod: For workpieces with special shapes, sliders and threaded rods can be used for clamping. The slider is usually located on the bed of the machine tool, and the height of the slider is adjusted by lifting the threaded rod and the nut, and the workpiece is clamped on the slider.
5. Self-made fixture: According to the special shape and processing requirements of the workpiece, a self-made fixture can be used to clamp the workpiece. Fixtures can be designed and customized according to workpiece needs to ensure proper clamping force and stability.
When clamping the workpiece, the following points need to be paid attention to:
1. Make sure that the fixture and clamping method can provide sufficient clamping force and stability to maintain the safety and precision of the workpiece.
2. Under normal circumstances, scratches or deformation on the surface of the clamped workpiece should be avoided.
3. Use suitable clamping tools and measuring tools to ensure the correct positioning and clamping of the workpiece in the fixture.
4. Regularly check the fixture and clamping force to ensure it is functioning properly, and make adjustments and maintenance as needed.
In short, choosing the appropriate clamping method needs to be evaluated according to the specific workpiece shape, weight, processing needs and other factors, and follow the recommendations and guidance of the machine tool and fixture manufacturer. Ensuring the stability and safety of workpiece clamping is crucial to the machining quality of CNC vertical lathes.