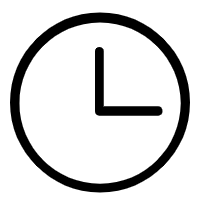
The spindle orientation of CNC machine tools is an important part of ensuring machining accuracy. Spindle orientation adjustment: Spindle orientation adjustment refers to adjusting the position of the spindle so that it is aligned with other parts of the machine tool to ensure stability during the machining process. Here are the steps to adjust spindle orientation:
1. Turn on the power of the CNC machine tool and start the spindle.
2. Enter the CNC system operation interface and select the spindle orientation function.
3. Use the adjustment button on the operation panel to manually adjust the position of the spindle.
4. Use high-precision measuring instruments such as laser interferometers to detect the accuracy of spindle orientation.
5. Based on the measurement results, fine-tune the position of the spindle until it meets the processing requirements.
Spindle orientation diagnosis method: During the spindle orientation adjustment process, various problems may occur that affect the adjustment effect. Here are tips for diagnosing spindle orientation problems:
1. Check whether the CNC system parameter settings are correct, including spindle orientation angle, motor parameters, etc.
2. Check whether the spindle motor is working properly, including motor bearings, motor coils, etc.
3. Check whether the spindle encoder is working normally, such as the encoder connection cable, signal processing module, etc.
4. Use the diagnostic tool to check whether the communication between the CNC system and the spindle is normal.
5. Check the installation accuracy of the machine bed, worktable and other components to ensure there is no looseness.
Through the above adjustment and diagnosis techniques, the accuracy of the spindle orientation of CNC machine tools can be effectively guaranteed and the processing quality and efficiency can be improved. During use, spindle orientation inspection and maintenance should be carried out regularly to ensure that the CNC machine tool is always in good working condition.