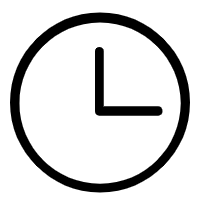
The direction and application point selection of the clamping force of CNC lathes are crucial to ensure the stability and accuracy of workpiece processing. The following are some general principles for selecting the direction and point of action of clamping force on CNC lathes:
1. Direction of clamping force:
Radial clamping: On CNC lathes, radial clamping is usually used, that is, the direction of the clamping force is perpendicular to the axial direction of the workpiece. This helps prevent radial movement of the workpiece during cutting and improves machining accuracy.
Axial clamping: The axial clamping method of CNC lathe is that the direction of the clamping force is parallel to the axial direction of the workpiece. This method is often used to ensure that the length of the workpiece is stable during processing, especially for longer workpieces.
2.Clamping point selection:
Workpiece outer diameter: If the outer diameter of the workpiece is the main machining surface of a CNC lathe, the clamping point should be selected on the outer diameter of the workpiece. This helps prevent the workpiece from rotating or wobbling during the cut.
Inner diameter of workpiece: If the inside of the workpiece needs to be processed on a CNC lathe, the clamping point can be selected on the inner diameter of the workpiece. This ensures that the workpiece does not move unsteadily during cutting.
Parallel plane: The CNC lathe clamping point can also be selected on the parallel plane of the workpiece to ensure the stability of the workpiece during the cutting process.
3. Symmetry considerations:
If the CNC lathe workpiece is symmetrical, the direction and action point of the clamping force can be selected so that the workpiece remains symmetrical relative to the fixture. This helps even out the clamping force and prevents the workpiece from tilting or deforming during clamping.
4. Clamping force size:
The clamping force of the CNC lathe should be large enough to ensure that the workpiece does not move during the cutting process, but at the same time, care should be taken not to be too large to avoid unnecessary deformation or damage to the workpiece.
5. Consideration of cutting direction:
Considering the direction of CNC lathe cutting force, the selection of clamping points and clamping force should also consider the force and reaction force during the cutting process to ensure clamping stability.
In general, the selection of clamping force direction and application point requires reasonable planning based on the specific workpiece geometry, machining process, and fixture design. In actual applications, some experimentation and adjustment are usually required to obtain the best clamping effect.