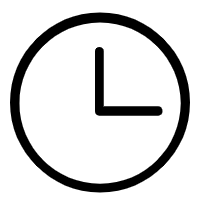
The methods to prevent tool breakage in CNC milling machines mainly include the following points:
1. The table of the CNC milling machine must be milled flat: The CNC milling machine ensures that the table is flat, which can avoid uneven force on the tool caused by uneven table during processing, thereby reducing the risk of tool breakage.
2. The plate is firmly fixed: Before carving, the CNC milling machine must use vacuum adsorption or other methods to firmly fix the plate. If there is no vacuum adsorption, special attention should be paid to fixing the plate horizontally and firmly to prevent the plate from moving or vibrating during processing, causing uneven force on the tool and breaking.
3. Correct tool installation: The CNC milling machine tool must be correctly installed and perpendicular to the spindle. This ensures that the tool is evenly stressed during processing and reduces the risk of tool breakage.
4. Check the spindle: Before the CNC milling machine is operated, it is necessary to check whether the spindle is firm and there must be no looseness. The looseness of the spindle of the CNC milling machine will cause the tool to shake during processing, increasing the risk of tool breakage.
5. Control the carving speed: The carving speed is also an important factor leading to tool breakage. Slow speed and high temperature will easily cause the knife to break; fast speed and high resistance will also easily cause the knife to break. Therefore, during processing, the carving speed must be reasonably controlled according to factors such as the thickness and material of the plate to reduce the risk of knife breakage.
The above methods can effectively reduce the risk of knife breakage in CNC milling machines and improve processing efficiency and product quality. At the same time, during the operation, CNC milling machine operators also need to stay focused and abide by the operating procedures to ensure the safe operation of the CNC milling machine.