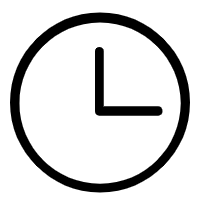
Damage to the CNC lathe spindle is a serious problem. To address this failure, a series of effective measures need to be taken to avoid and solve it. Here are some key measures:
1. Preventive and maintenance measures:
Reasonable bearing selection: CNC lathe bearing selection should consider the bearing's rated load capacity and the actual load in the working environment, and select the bearing type suitable for the spindle to reduce damage caused by overload or improper use.
Strengthen lubrication management: CNC lathes regularly replace grease to keep lubrication flowing to reduce friction and wear. At the same time, the working status of the lubrication system should be checked to ensure its normal operation.
Keep the spindle box clean: Clean the CNC lathe spindle box regularly to prevent impurities from entering the bearings and reduce wear and failure caused by impurities.
Strengthen daily maintenance: Carry out daily inspection and maintenance of CNC lathes to discover and eliminate potential faults in a timely manner. This includes checking the cleanliness and fit of the shaft hole and tool holder of the CNC lathe spindle, as well as checking the heat generation and rotation accuracy of the spindle.
2. Troubleshooting measures:
Problems with CNC lathe spindle heating and reduced rotation accuracy: First, replace the front-end bearing of the spindle, use qualified grease, and adjust the bearing clearance. Secondly, grind the positioning surface of the tapered hole in the CNC lathe spindle to ensure that the contact surface with the tool holder is not less than 90%. In addition, replace the spring of the clamping device and adjust the preload of the bearing.
The problem that the spindle does not rotate: Check whether the transmission belt of the CNC lathe is broken or whether the machine tool is in neutral, check whether the three-phase power supply to the spindle is missing or reversed, check whether the circuit connection is correct, and check whether the system has a corresponding spindle control signal output wait.
3. Other matters needing attention:
Regularly conduct comprehensive inspections of CNC lathes, including electrical systems, mechanical systems and cooling systems, to ensure the normal operation of each component.
During the operation of CNC lathes, the processing technology must be reasonably arranged to avoid overload work to extend the service life of the spindle.
To sum up, the preventive measures and troubleshooting measures for CNC lathe spindle damage are multi-faceted and need to be considered and operated from multiple perspectives such as selection, lubrication, cleaning, and maintenance. Only in this way can the normal operation of the CNC lathe spindle be ensured and the machining accuracy and efficiency improved.