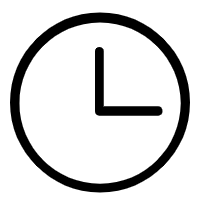
High-rigidity vertical lathe is a high-precision and high-efficiency mechanical equipment widely used in various manufacturing industries. However, during the mechanical processing process, cutting vibration will affect the processing quality and processing efficiency, and reduce the life of the equipment. Therefore, how to reduce cutting vibration is an important issue in the development of high-rigidity vertical lathes.
Generally speaking, there are two methods to reduce cutting vibration. One is to optimize the structure and design of the equipment to make the equipment more rigid and stable; the other is to optimize the processing technology and reduce cutting vibration by reducing cutting force.
In the development of high-rigidity vertical lathes, the first method is more important. First of all, strengthening the rigidity and stability of the equipment can reduce the deformation and vibration of the equipment during processing and improve processing accuracy and efficiency. Secondly, by optimizing the layout and structure of bearings and transmission components, transmission errors and friction are reduced, and the working stability and reliability of the equipment are improved.
Specifically, methods to reduce cutting vibration include the following aspects:
1. Optimize the machine tool structure. By improving the stability and rigidity of the machine tool, reducing vibration and deformation, it enhances its load-bearing capacity and stability. For example, the use of wear-resistant materials, reinforced beams and rigid support designs of the machine bed, etc.
2. Choose the tool and tool handle reasonably. Factors such as tool rigidity, length, material, and machining accuracy all affect cutting vibration. Therefore, when selecting tools and toolholders, the selection should be based on the specific cutting task and the characteristics of the machine tool.
3. Use damping technology. By setting dampers on the equipment or using appropriate materials for damping, the transmission of vibration can be reduced and the resonance phenomenon of the equipment can be alleviated, thereby improving the stability and work efficiency of the entire system.
4. Add adaptive control system. The advanced adaptive control system can monitor and analyze the vibration and parameters of the machine tool in real time, and automatically adjust and optimize during the processing to reduce cutting vibration and improve processing quality.
Combining the above methods can effectively reduce cutting vibration, improve processing accuracy and efficiency, and reduce equipment operating costs and failure rates. This has a positive role in improving the competitiveness of the manufacturing industry and industrial development.