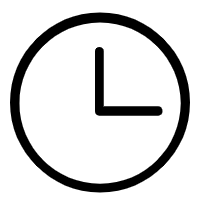
Fault diagnosis of precision CNC lathes is a systematic process that needs to follow some basic principles. The following are the general principles for fault diagnosis of precision CNC lathes:
1. Observe and record: First, carefully observe the fault phenomenon of the CNC lathe and record relevant information, including the time, frequency, environmental conditions, etc. of the fault.
2. Systematic analysis: CNC lathes systematically compare and analyze fault phenomena and possible causes. For complex lathe systems, failures may be caused by mechanical, electrical, hydraulic, pneumatic and other aspects.
3. Step by step elimination: The CNC lathe starts with the most likely cause and gradually eliminates it, reducing the scope of the fault step by step. This requires judging possible causes based on experience and technical knowledge, and conducting inspections and tests one by one.
4. Utilize diagnostic tools: CNC lathes use appropriate diagnostic tools and equipment to help determine the cause of the failure. For example, use equipment such as an oscilloscope, multimeter, fault code reader, etc. to check circuits and sensors.
5. Reference documents and manuals: Consult the technical manual, maintenance manual and other documents provided by the manufacturer to understand the working principle, structure and common troubleshooting methods of the lathe.
6. Pay attention to safety: When performing fault diagnosis and maintenance on CNC lathes, you must pay attention to safety. Ensure that the lathe is in a safe condition and follows relevant operating procedures and safety standards.
7. Teamwork: If the CNC lathe encounters a complex fault or requires special skills to repair, you can consider working with a team or seeking help from professionals.
8. Continuous improvement: CNC lathes need to conduct fundamental analysis and improvements for frequently occurring faults to avoid similar faults from happening again and improve the stability and reliability of lathes.
In general, fault diagnosis of precision CNC lathes requires a combination of experience, technical knowledge and a systematic approach. Through careful analysis and judgment, the cause of the failure can be effectively determined and corresponding measures can be taken for repair and improvement.