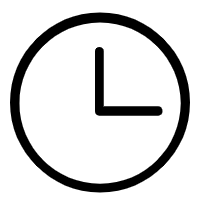
Reverse error (also known as hysteresis error or return error) is the error caused by the hysteresis effect of the mechanical transmission system and control system when the index control system changes the direction of movement. This error may have some impact on the machining accuracy and efficiency of precision CNC lathes. The following are some possible impacts:
1. Reduced processing accuracy: The reverse error will cause a difference between the actual CNC lathe tool position and the expected position, thereby reducing the processing accuracy. Especially when high-precision machining is required, this error may have a negative impact on the size and surface quality of the workpiece.
2. Poor surface quality: Reverse error may cause the CNC lathe tool to produce irregular trajectories on the workpiece surface, thus affecting the surface quality. This can be a problem for machining tasks that require smooth surfaces.
3. Increased tool wear: Due to reverse error, CNC lathe tools may move on different trajectories, which may increase tool wear and loss. Increased tool wear may require more frequent tool changes, affecting productivity.
4. Extension of processing time: In order to compensate for the reverse error of the CNC lathe, the system may need to adopt a slower speed or perform more corrective movements, which may lead to an extension of the processing time.
5. Reduced tool life: Since reverse errors may lead to irregular cutting conditions on CNC lathes, the tool may face greater impact and load, thereby reducing the tool life.
In order to reduce the impact of reverse error on precision CNC lathes, the following measures can be taken:
1. Regular calibration: Calibrate the CNC system regularly to ensure its consistency with actual motion.
2. Use high-quality transmission components: Select and use high-quality transmission components and mechanical components to reduce the hysteresis effect of the mechanical system.
3. Optimized control algorithm: Adopt advanced control algorithm to reduce the response time and hysteresis effect of the system.
4. Monitoring and maintenance: Regularly monitor system performance and perform timely maintenance and repairs to ensure that the system remains in optimal condition.
By taking these measures, the adverse impact of reverse error on the processing quality and efficiency of precision CNC lathes can be reduced.