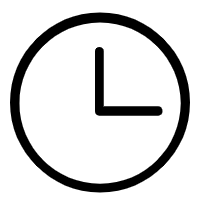
Precision testing of CNC vertical lathes is an important task for testing machine tools, and it is also an important link in ensuring the quality of machine tools. The detection results will directly affect the machining accuracy, production efficiency, and service life of the machine tool. This article will introduce the relevant standards and methods for precision testing of CNC vertical lathes.
The accuracy testing of CNC vertical lathes is mainly divided into two aspects: static testing and dynamic testing. Static inspection is the inspection of a machine tool in a static state, including measuring the dimensions and shapes of various parts of the machine tool, such as guides, tool holders, spindles, etc. Dynamic detection is the detection of indicators such as cutting force and vibration during machine tool processing.
The accuracy testing items of CNC vertical lathes mainly include the following aspects:
1. CNC system accuracy detection: such as system position accuracy, repeated positioning accuracy, etc;
2. Spindle accuracy detection: such as spindle rotation accuracy, runout, etc;
3. Inspection of straightness of the moving table (lathe bed): such as straightness, parallelism, verticality, etc. of the moving table;
4. Rail inspection: such as the flatness and parallelism of the rail;
5. Knife holder inspection: such as whether the knife holder is balanced and firmly fixed;
6. Detection of coolant system: such as coolant system flow rate, pressure, etc.
The accuracy detection indicators of CNC vertical lathes mainly include the following aspects:
1. Position accuracy: The numerical control system guides the operation of the machine tool, and its position accuracy directly affects the dimensional accuracy of the machined parts;
2. Repetitive positioning accuracy: Cutting is continuously carried out, and the tool must be able to accurately return to the set position to avoid the need for original machining of the workpiece;
3. Spindle rotation accuracy: The spindle not only needs to ensure smooth rotation, but also needs to achieve small deviation of the rotation axis to ensure that the final size error of the workpiece is not large;
4. Jumping amount: When setting the cutting, it is required that there is an irregular shape or periodic change around the spindle, and the cutting force cannot generate consistent force, resulting in oscillation, which leads to a decrease in cutting performance and forming accuracy;
5. Moving table straightness: The lathe bed needs to be kept parallel within a certain accuracy range and maintain a certain forward or backward verticality;
6. Rail flatness: The straightness of the rail is maintained within a certain range and the parallelism between the lines is ensured;
7. All indicators such as parallelism, verticality, and levelness must meet the requirements of relevant national standards.
The accuracy testing of machine tools is a key task to ensure their performance, machining accuracy, and service life. Relevant personnel should fully recognize its importance and conduct testing according to standard specifications.