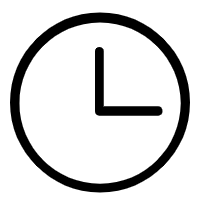
In the specific production of vertical machining centers, various problems usually arise. In order to improve production efficiency and ensure production quality, the network Xiaobian summarizes the common problems of vertical machining centers, and provides reasonable and effective improvement methods, so that everyone can adjust the cutting speed, feed and cutting depth more accurately.
Common problem 1: Workpiece overcut.
The external causes of workpiece overcut are generally insufficient turning tool hardness or improper external dimensions, while the internal causes may be irregular operation, improper setting of cutting parameters, and uneven setting of cutting amount, resulting in large tolerances, resulting in workpiece overcut and production errors.
In view of this problem, the number should be kept unified as much as possible when adding the corner clearing procedure, the specific operation of the turning tool should be as large as possible, and the SF function of the vertical machining center should be used to fine-tune the degree and gradually achieve a good cutting effect.
Common problem 2: Point of inaccuracy.
In the middle is the step of determining the origin of the machining center. It can be said that the machining center is inseparable from this step for the specific operation of other specific operations. In addition to manual operation by the operator, burrs around the mold shell, four non-vertical edges, and the magnetism of the centering rod can cause inaccurate centering.
The machining center should demagnetize the centering rod before centering the mold shell. Manual operation should be checked multiple times, and each point should be kept at the same point and the same height as much as possible; Be sure to check the table to see if the four sides of the mold housing are vertical.
FAQ 3: Collision.
There is a saying in the workshop of the machining center: all good technology is knocked out by an airplane. Although collisions are difficult to avoid now, as a qualified machining center operator, he should be able to control the preventable collision factors within the scope of prevention. There are many causes of collisions, so we must control preventable factors in advance.
Factors that can prevent collisions include insufficient safety height setting; There are errors in the length and specific production depth of the turning tool on the single upper part of the CNC program, and errors in the depth Z-axis data retrieval and the specific Z-axis data retrieval; Error setting coordinates during programming.
Therefore, the height of the workpiece needs to be measured to ensure that the safe height of the vertical machining center is above the workpiece. The turning tool on the CNC program sheet should be consistent with the turning tool of the specific program, and the program sheet should be exported with drawings as much as possible; Carefully measure the production depth on the workpiece and write clearly the length of the turning tool and the insert length on the program sheet. The specific Z-axis data retrieval should be clearly written on the program sheet, and this specific operation is manual. It should be checked several times to make sure there are no problems.
The emergence of vertical machining centers has brought the CNC production capacity of the production workshop to a new period. The specific operation of vertical machining centers requires further active learning and diligent exploration.