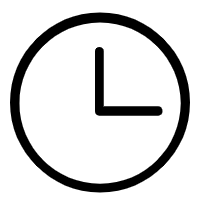
The tool setting skill of CNC lathe is to ensure that the tool is correctly aligned with the workpiece and achieve precise cutting during machining. The following are some commonly used CNC lathe tool setting skills:
1. Tool setting: Before setting the tool on the CNC lathe, it is necessary to ensure that the geometric parameters of the tool are set correctly. This includes tip-to-nose length, tool offset, cutting edge length, etc. According to the different types of tools and the requirements of the workpiece, adjust the length and position of the tool appropriately.
2. Zero-point tool setting: Zero-point tool setting refers to aligning the tool with the reference zero position on the workpiece. Commonly used zero points include the starting point, center point or edge point of the workpiece size. After setting the correct coordinate system and coordinate origin in the NC program, use an inductive measuring tool (such as an inductive tool length meter) or an auxiliary tool (such as an auxiliary zero block) to determine the zero point position.
3. Manual tool setting: manual tool setting is a common step before automatic tool setting. By manually operating each axis of the CNC lathe, the tool is gradually moved into contact with the workpiece, and adjusted visually or manually to make the tool parallel, vertical or inclined to the workpiece, and make smooth contact.
4. Automatic tool setting: Automatic tool setting is a tool setting operation using the automatic function of the CNC lathe. Through the tool setting function in the NC program, the lathe will automatically move the tool to the set tool setting position, and record the difference between the actual position and the set position. According to the difference, a compensation adjustment can be made to ensure the accuracy of the cutting position.
5. Cutting test run: After the tool setting is completed, a cutting test run is performed to verify the accuracy of the tool position and cutting parameters. By gradually increasing the cutting depth, speed and feed rate, observe the chip shape, machined surface quality and tool sound and other indicators during the cutting process to judge whether the processing conditions are suitable.
6. Regular inspection and calibration: tool setting of CNC lathe is a continuous process. Therefore, it is very important to check and calibrate the knife regularly. Inspect tool for wear, feature size and mounting, and repair or replace as necessary. At the same time, regularly check the accuracy of each axis of the CNC lathe and the accuracy of zero return to ensure the accuracy and stability of tool setting.
These tool setting tips can help ensure good tool setting on CNC lathes, improving machining quality and efficiency. In actual operation, it is also necessary to adjust and optimize according to the specific CNC lathe model and processing requirements, combined with the operation manual and experience.