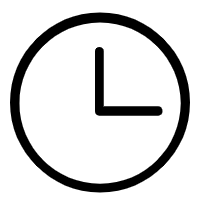
The accuracy inspection standards for CNC vertical lathes involve many aspects to ensure that the processing accuracy and performance of the machine tools meet the requirements. Here are some of the main inspection criteria:
Geometric accuracy detection:
Check the flatness of the machine tool work surface to ensure it is flat and smooth.
Check whether the angles generated by moving the spatial coordinates of the motion axis in different directions are vertical.
Check whether the center hole diameter of the spindle and the axis of the rotary axis are perpendicular to the machine tool work surface.
Check the table parallelism when the machine tool motion axis moves in the X and Y coordinate directions.
Check the parallelism of the T-shaped groove side of the moving table in the X coordinate direction.
Check the straightness of the movement of the spindle box along the Z-axis coordinate, etc.
These inspections are all to confirm whether the geometric accuracy of the machine tool is up to standard to meet the processing and production needs.
Position accuracy detection:
Positioning accuracy: Check whether the CNC machine tool table or other moving parts of the machine tool are at the set movement position during actual operation, whether they are consistent with the programming instructions, and whether they are consistent in position.
Repeated positioning accuracy: Check whether the workpiece positioning error range is within the allowable range when the machine tool is repositioned multiple times. It should generally be controlled within 0.015-0.02mm.
Straightness and flatness error:
The straightness error of CNC vertical lathe should be controlled within 0.02mm/m.
The flatness error should reach the standard of 0.025mm/m.
The control of these errors is to ensure that the machine tool can maintain stable accuracy during the machining process.
Speed error and radial offset error:
The standard for speed error is generally 1-1.5%.
The radial offset error should be controlled within 0.02mm.
Detection tools and precautions:
Commonly used testing tools include precision level, precision square box, dial indicator or micrometer, right angle meter, flat ruler, high-precision spindle mandrel and dial indicator rod magnetic base, etc.
At the time of inspection, the base of the machine tool should be fully cured.
During testing, errors in testing tools and testing methods should be minimized.
In accordance with relevant national standards, the machine tool should be preheated by first turning on the machine power, and allowing each coordinate axis of the machine tool to reciprocate several times, so that the spindle runs at medium speed for several minutes before testing.
The accuracy level of the inspection tool used is one level higher than the geometric accuracy being measured.
To sum up, the accuracy inspection standards of CNC vertical lathes involve many aspects, including geometric accuracy, position accuracy, straightness and flatness errors, rotational speed errors and radial offset errors, etc. During the testing process, it is necessary to use appropriate testing tools and pay attention to some key matters to ensure the accuracy and reliability of the testing results.