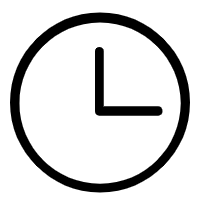
There may be many reasons for the collision of CNC lathes during operation, mainly including the following points:
1. Incorrect input of tool diameter and length: If the tool diameter and length are entered incorrectly during programming, a collision with the workpiece or other parts may occur during the actual cutting process.
2. Incorrect input of relevant geometric dimensions such as workpiece size: If the relevant parameters such as the size and shape of the CNC lathe workpiece are entered inaccurately, the cutting trajectory may not be consistent with expectations, thereby causing a collision.
3. Incorrect initial position positioning of the workpiece: When the CNC lathe workpiece is clamped to the machine tool, if the initial position positioning is inaccurate, it may also cause a collision during the cutting process.
4. Incorrect setting of the workpiece coordinate system of the CNC lathe: If the workpiece coordinate system is set incorrectly, the cutting path will not match the actual position of the workpiece, resulting in a collision.
5. Machine zero reset during processing: During the processing of the CNC lathe, if the machine zero is reset or changed, it may cause the cutting path to deviate and cause a collision.
6. Operator error: If the CNC lathe operator operates improperly or negligently during the execution of the program, tool change, etc., it may also cause a collision.
In order to avoid collisions on CNC lathes, CNC lathe operators need to fully master the machine tool operating skills, carefully check the programming parameters and workpiece dimensions, ensure that the initial position of the workpiece is accurate, and strictly follow the operating procedures. At the same time, CNC lathes also need regular maintenance and inspection to ensure that all functions are normal and reduce the possibility of failures.