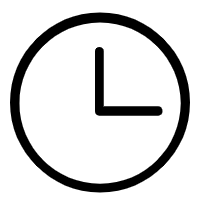
In the processing process of modern CNC lathes, it is very important to keep the temperature of the workpiece and the tool stable, which can effectively reduce the wear of the tool and the quality problems of the workpiece surface. For this reason, cooling methods also become crucial. So, what are the cooling methods for CNC lathes?
The first is water cooling. CNC lathes can use water cooling to keep the temperatures of the cutting tools and workpieces stable. The water cooling method is a method of introducing water into the processing area of the tool and workpiece through pipelines to cool them. Among them, water cooling can not only keep the temperature of the object stable during the processing process, but also clean the surface, improving the quality of the processed surface.
The second is the gas cooling method. The gas cooling method is specially designed to maintain the processing quality of CNC lathes. In this way, the machining area is cooled by blowing air onto the tool and workpiece surfaces. The main advantage is that it has high controllability, can easily adjust the air volume and temperature, and can also prevent cutting fluid contamination. At the same time, because there is no need to prepare coolant, the gas cooling method is also more environmentally friendly.
The third is the oil mist cooling method. Oil mist cooling is usually used for cooling required in high-speed cutting. In this way, oil is added to the processing area to form an oil mist. The oil mist will form a protective film between the tool and the workpiece, effectively reducing tool wear and preventing high temperatures from being generated during the cutting process.
The fourth is dry cooling method. Dry cooling uses the environment to control the temperature stability of the tool and workpiece, rather than using coolant. This method is mainly aimed at workpieces and tools whose processing temperatures are relatively low. Dry cooling is one of the safest cooling methods. However, it should be noted that its impact on the machined surface directly leads to quality problems.
The cooling methods of CNC lathes are very diverse, and each method has its own characteristics and applications. During use, appropriate and reliable cooling methods should be selected according to the different needs of the processed materials to improve processing quality and work efficiency.