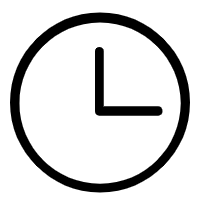
The impact of blank materials on CNC vertical lathes is mainly reflected in the following aspects:
1. Processing accuracy: The physical and chemical properties of CNC vertical lathe blank materials, such as hardness, toughness, thermal expansion coefficient, etc., will directly affect the processing accuracy of CNC vertical lathes. For example, blank materials with higher hardness require higher cutting forces and cutting speeds, which may cause vibration and deformation of the machine tool, thereby affecting the processing accuracy.
2. Tool wear: The hardness and wear resistance of CNC vertical lathe blank materials have a direct impact on tool wear. Blank materials with higher hardness will accelerate tool wear, require more frequent tool replacement, and increase processing costs.
3. Processing efficiency: The processing performance of CNC vertical lathe blank materials will affect the processing efficiency of CNC vertical lathes. If the cutting performance of the blank material is poor, it will take longer processing time and higher energy consumption to complete the processing task.
4. Processing surface quality: The internal structure and chemical composition of CNC vertical lathe blank materials will affect the surface quality after processing. For example, blank materials containing more impurities or bubbles may have problems such as surface unevenness and cracks after processing.
Therefore, when selecting blank materials for CNC vertical lathes, it is necessary to comprehensively consider factors such as the physical and chemical properties of the materials, processing performance, and cost to ensure that the CNC vertical lathe can complete the processing tasks efficiently and accurately. At the same time, it is also necessary to select appropriate blank materials according to specific processing requirements to obtain the best processing effect.