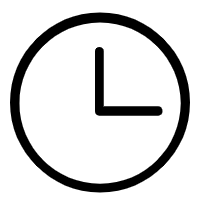
CNC lathe tool setting is an important link in CNC machining, which involves the accurate conversion between the workpiece coordinate system and the machine tool coordinate system. The following are several main methods and related techniques for CNC lathe tool setting:
1. Knife setting method
Trial cutting method:
Select the manual operation mode of the CNC lathe, start the spindle component, and try to cut the outer circle of the workpiece without moving in the X direction.
Stop the spindle operation and measure the outer diameter of the workpiece.
Change the machine tool operating mode and enter the previously measured value for measurement.
This method is simple and convenient, but it will leave cutting marks on the surface of the workpiece and the tool setting accuracy is low.
Tool setting method for feeler gauge, standard mandrel and block gauge:
CNC lathes add a feeler gauge (or standard mandrel, block gauge) between the tool and the workpiece.
Make sure that the feeler gauge cannot twitch freely. Note that the thickness of the feeler gauge should be subtracted when calculating coordinates.
This method will not leave marks on the surface of the workpiece, but the tool setting accuracy is not high enough.
Tool setting methods for tools such as edge finders, eccentric rods, and axis setters:
The CNC lathe operation steps are similar to the trial cutting tool setting method, but the tool is replaced by an edge finder or eccentric rod.
When using the edge finder, care must be taken to allow the steel ball part of the edge finder to be in slight contact with the workpiece.
Transfer (indirect) tool setting method: often used in certain specific situations to perform indirect tool setting through other tools or methods.
Top tool setting method: used under certain specific workpieces or processing requirements.
Dial indicator (or dial indicator) tool setting method: often used for tool setting of round workpieces.
2. Knife setting skills
Check the lathe: Make sure that the parameters of the lathe, such as spindle speed, feed speed, etc., meet the requirements. At the same time, check the wear of the tools and replace seriously worn tools in a timely manner.
Workpiece preparation: Clean the surface of the CNC lathe workpiece to ensure that there are no debris and cutting oil stains to improve the accuracy of tool setting.
Choose appropriate tool setting tools: such as auxiliary tool setting instruments, tool setting seats, etc. to ensure the stability and accuracy of the tool setting process.
CNC lathe determines the reference position of the tool: Before performing tool calibration, the reference position of the tool must be clear for subsequent adjustments.
Tool position and attitude adjustment: Adjust the position and attitude of the tool according to the workpiece contour and requirements to ensure accuracy and stability during processing.
Tool setting test run: After completing the tool position and attitude adjustment, perform a tool setting test run to check whether the tool is correctly set. During the test run, pay attention to selecting the appropriate feed speed and spindle speed, observe the cutting conditions, and check whether the shape and size of the processed workpiece meet the requirements.
To sum up, CNC lathe tool setting needs to comprehensively consider a variety of methods and techniques, choose the appropriate method according to the specific processing needs and workpiece characteristics, and follow certain techniques and precautions to ensure the accuracy and efficiency of the tool setting process. sex.