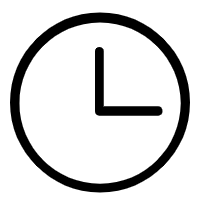
Checking the accuracy of a CNC lathe is one of the important steps to ensure that it can meet processing requirements and maintain stability and accuracy. The following are commonly used methods for checking the accuracy of CNC lathes:
1. Geometric accuracy detection:
Straightness detection: CNC lathes use straightness measuring instruments or laser interferometers to detect the straightness of each axis of the machine tool to ensure that the axis movement is smooth and the straightness is within the allowable range.
Parallelism detection: CNC lathes use parallelism measuring instruments to detect the parallelism between each axis of the machine tool to ensure that the parallelism between each axis meets the requirements.
Verticality detection: CNC lathes use verticality measuring instruments to detect the verticality of each axis of the machine tool to ensure that the verticality between each axis meets the requirements.
Axial distance detection: Detect the axial distance between the CNC lathe worktable and the spindle to ensure the accuracy of the workpiece clamping position.
2. Position accuracy detection:
CNC lathe position accuracy detection includes two aspects: positioning accuracy and repeat positioning accuracy. CNC lathe positioning accuracy detection evaluates the positioning accuracy of the machine tool by measuring the deviation between the actual position of the workpiece and the programmed position at different positions. The repeated positioning accuracy test of CNC lathes measures the actual position of the workpiece multiple times at the same position to evaluate the stability and accuracy of the machine tool during repeated positioning.
3. Roundness and cylindricity detection:
CNC lathes use measuring instruments (such as micrometers, outer diameter measuring instruments, etc.) to measure the processed cylindrical surface to evaluate whether its roundness and cylindricity are within the allowable range.
4. Surface roughness detection:
CNC lathes use surface roughness measuring instruments (such as surface roughness meters) to measure the processed surface and evaluate whether its surface quality meets the requirements.
5. Tool deviation detection:
CNC lathes detect the geometric parameters of the tool (such as tool tip arc radius, tool tip angle, etc.) to ensure that the tool geometry meets the design requirements.
6. Processing test:
CNC lathes conduct actual processing tests, process typical workpieces and measure their dimensional and geometric tolerances to evaluate the processing capabilities and accuracy of the machine tools.
The above methods are often used in combination to comprehensively evaluate the accuracy performance of CNC lathes. Depending on the processing requirements and machine tool model, other specific inspection methods and tools can also be used.