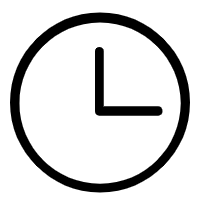
CNC vertical lathe is a high-precision and high-efficiency processing method that is increasingly used in modern mechanical processing. When performing CNC vertical lathe processing, you need to pay attention to the following requirements.
First, choose the appropriate workpiece material. CNC vertical lathes are suitable for processing metal parts with high precision requirements, such as shaft shells, gears, etc. When selecting the workpiece material, it needs to be selected according to the processing requirements and the capabilities of the machine tool equipment to ensure the processing effect and the quality of the workpiece processing.
Secondly, the size of the workpiece must be accurately measured. CNC vertical lathe processing requires very precise dimensional control, so the workpiece needs to be accurately measured before processing to facilitate the writing of processing programs and adjustment of processing parameters. The accuracy of dimensional control directly affects the accuracy and quality of processed parts.
In addition, CNC vertical lathe processing also requires reasonable parameters such as feed, speed and cutting depth. This is the key to ensuring the quality of workpiece processing. When setting these parameters, they should be adjusted according to factors such as specific machining tasks and workpiece materials. It should be noted that most workpieces require multiple processes for processing, and it is necessary to design a reasonable processing plan and make timely adjustments to the processing process.
Finally, perform maintenance and upkeep on machine tool equipment. CNC vertical lathes involve complex machine tools and precision tools, so they require regular maintenance and upkeep. During the processing process, the status of the machine tool should be checked in time, and adjustments and maintenance operations should be performed according to the situation to ensure the life and accuracy of the machine tool equipment and cutting tools.
In short, CNC vertical lathe processing requires ensuring requirements and details in many aspects. Only with clear planning and strict control of the processing process can the processing quality and workpiece formation be guaranteed.