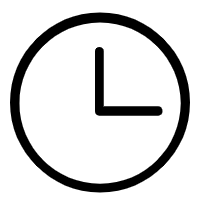
CNC vertical turning is an efficient and high-precision processing method. In the CNC vertical lathe cutting process, the size and stability of the cutting amount have a crucial impact on the processing effect and processing quality. So, what is the impact on CNC vertical lathe cutting consumption? Let’s discuss it together.
1. Tool material, edge shape and size: The tool is one of the most important components in CNC vertical lathe processing. The advantages and disadvantages of its material, edge shape and size directly affect the size, stability and effect of cutting.
2. Workpiece material: The workpiece material has a great influence on the cutting amount. Different workpiece materials have different requirements on the wear rate and effect of the cutting tool.
3. Cutting speed: Cutting speed refers to the linear speed of the tool relative to the workpiece, and is also one of the factors that affects the cutting amount. If the cutting speed is too high or too low, the cutting amount will be unstable.
4. Feed speed: Feed speed refers to the processing speed of the tool along the surface of the workpiece when cutting. If the feed speed is too low, the tool will cut too deep, thereby increasing the cutting amount; if the feed speed is too high, the cutting amount will be increased. Unstable.
5. Cutting fluid: Cutting fluid plays the role of cooling and lubrication during the cutting process, which can reduce cutting temperature, extend tool life, and improve processing quality. Different cutting fluids also have different effects on cutting dosage.
To sum up, CNC vertical turning cutting consumption is affected by many factors. Only by optimizing the cutting tool, workpiece, cutting speed, feed speed and cutting fluid can we achieve better processing results and processing quality. At the same time, the tool life is extended and the production efficiency is improved.