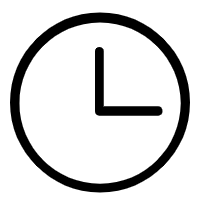
The tool setting principle of CNC milling machine is mainly to measure the relative position of the workpiece and the tool through the probe to determine the distance between the tool and the workpiece surface, so as to determine the cutting depth and position of the tool. Specifically, tool setting includes the following main steps and principles:
1. When the CNC milling machine sets the tool, the tool position point (usually the center of the tool end ball) coincides with the tool setting point, which is the basis for ensuring accurate measurement.
2. The CNC milling machine determines the relationship between the programming origin and the reference point of the machine tool coordinate system. The programming origin is a fixed point on the workpiece set during programming, and the machine tool coordinate system reference point is a fixed point on the machine tool. The relationship between these two points needs to be clear.
3. The CNC milling machine determines the relative position relationship between the tool position point and the workpiece coordinate system through programming. CNC milling machine This usually involves moving the tool to a position a certain distance away from the workpiece surface, and then using the probe to gently touch the workpiece surface. At this time, the relative position of the tool and the workpiece can be read.
During the operation of the CNC milling machine, there are two common tool setting methods: one-time tool setting and multiple tool setting. One-time tool setting is usually performed using a dedicated tool setting instrument, including a probe and a digital display. First, manually move the tool to a position a certain distance from the workpiece surface and return the pointer of the digital display to zero. Then, gently touch the probe to the workpiece surface, and the reading of the digital display is the relative position of the tool and the workpiece. Adjust the position of the tool as needed so that the reading of the digital display reaches the required value to complete the tool setting.
In addition, data acquisition of CNC milling machines is the core link of tool setting. This is usually done with the help of tactile detection technology, such as mechanical switch contacts and capacitive sensors. This type of probe is installed at the spindle end and shares a position with the tool. When the probe contacts the workpiece and produces a small displacement, the transmitter will obtain the change in electrical parameters, convert it into position data, and directly output it to the tool offset register of the CNC system, thereby automatically establishing a coordinate mapping relationship.
It should be noted that the quality of tool setting directly affects the processing accuracy. As the first process, the quality of tool setting on CNC milling machines directly determines the precision of subsequent processing. Therefore, when performing tool setting operations, it is necessary to strictly follow the operating procedures to ensure the accuracy and stability of tool setting.