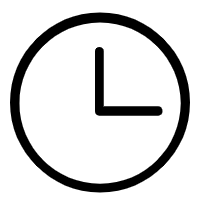
The processing sequence of CNC lathes usually follows certain principles to ensure processing efficiency, accuracy and workpiece quality.
1. Roughing first, then finishing:
Roughing: First, the CNC lathe performs roughing to quickly remove most of the machining allowance on the workpiece surface. This helps to improve the metal removal rate and provide uniform allowance for subsequent finishing.
Semi-finishing (if necessary): If the uniformity of the allowance left after roughing by the CNC lathe does not meet the requirements of finishing, semi-finishing needs to be arranged to make the finishing allowance small and uniform.
Finishing: After roughing and semi-finishing, the CNC lathe performs finishing. During finishing, the tool moves along the contour of the part in one pass to ensure the machining accuracy and surface roughness requirements of the part.
2. Near first, far later:
The "far" and "near" here refer to the distance of the processing part relative to the tool change point. When the CNC lathe performs roughing, the part close to the tool change point is processed first, and the part far from the tool change point is processed later. This can shorten the tool movement distance, reduce the idle travel time, and help maintain the rigidity of the blank or semi-finished parts and improve their cutting conditions.
3. Internal and external intersection:
For parts with both internal surfaces (inner mold, inner cavity) and external surfaces, the internal and outer surfaces should be rough-machined first, and then the internal and outer surfaces should be fine-machined. Usually, the inner mold and inner cavity are machined first, and then the outer surface is machined. This is because it is difficult to control the size and shape of the inner surface, and the tool rigidity is poor, and the durability of the tool tip (edge) is easily affected by cutting heat and reduced.
4. Datum first, then others:
The processing of CNC lathe parts generally starts with the processing of the precision datum, and then the precision datum is used to locate and process other major and minor surfaces. This helps to ensure the accuracy and stability of subsequent processing.
5. Reduce the number of tool changes:
CNC lathes use the same turning tool to process all parts that can be processed as much as possible, and then change the tool to process other parts. This can shorten the auxiliary time of processing and improve production efficiency.
6. Process the positioning surface first:
The processing of the CNC lathe, that is, the processing of the previous process, can provide the finishing datum and suitable clamping surface for the subsequent process. This helps ensure the stability and accuracy of subsequent processing.
7. Process the plane first and then the hole:
CNC lathes process simple geometric shapes first and then complex geometric shapes. This helps reduce the difficulty of processing and improve processing efficiency.
In summary, the processing sequence of CNC lathes is a process that comprehensively considers processing efficiency, accuracy and workpiece quality. By following the above principles, the smooth progress of the processing process and the high-quality completion of the workpiece can be ensured.