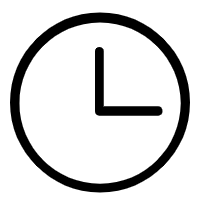
The main reasons for the wear of turning tools on CNC lathes are as follows:
1. The tool material is not suitable or the hardness is not enough: If the CNC lathe tool material is not suitable for the material or workpiece being processed, or its hardness is insufficient, it will cause the tool to wear faster. For example, when machining high-hardness workpieces, you need to use sufficiently hard tool materials, otherwise the tools will wear out quickly.
2. Improper cutting conditions: CNC lathe cutting speed and feed rate are too high, or the cutting area is too large, which may cause the tool to overheat and accelerate wear. In addition, the blade shape or the working material itself makes the shear angle of the chips too small, which may also lead to increased tool wear.
3. Improper operation: For example, suddenly stopping the machine tool during the cutting process, or the turning tool falling during operation, or holding multiple tool bars at the same time to cause the cutting edges to collide with each other, may cause damage to the tool.
4. Excessive wear: If the CNC lathe tool is not replaced when it reaches about 80% of normal wear, excessive wear will cause the tool performance to decrease or even be damaged.
3. Rake face wear: Friction and diffusion on the rake face will cause wear. This wear can be caused by contact between the cutting and workpiece materials and the spread of heat to the area. If the tool material is too soft, the cutting speed is too high and the feed rate is too large during processing, it will also aggravate the wear of the rake face.
6. Plastic deformation: Under the action of high temperature or high stress, the cutting edge of a CNC lathe may undergo plastic deformation, causing tool wear. Factors such as excessive CNC lathe cutting speed and feed speed, the effect of hard points in the workpiece material, and too soft tool materials may cause plastic deformation.
7. Built-up edge: The adhesion of CNC lathe workpiece material to the tool will form built-up edge, which will not only reduce the quality of the machined surface, but may also change the shape of the cutting edge, eventually leading to chipping.
In order to reduce the wear of turning tools, the following measures can be taken:
1. Choose the appropriate tool material and hardness.
2. Optimize cutting conditions, including reducing cutting speed and feed speed, and selecting appropriate cutting depth and cutting method.
3. Follow correct operating procedures to avoid accidental collisions and sudden shutdowns during operation.
4. Check the tool wear regularly and replace the tool in time when the tool is worn to a certain extent.
Through these measures, the wear of CNC lathe turning tools can be effectively reduced, and the processing efficiency and workpiece quality can be improved.