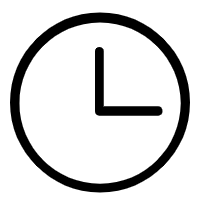
The chassis of a vertical lathe can adopt different designs in smooth form. Common smooth forms include:
1. Sliding guide: This is one of the most common forms of chassis smoothness. Sliding guides are usually made of metallic materials, such as cast iron or steel. The sliding surface formed between the guide rail and the slider mounted on the base is usually precision machined to provide smooth movement and high positioning accuracy.
2. Rolling guides: Rolling guides use rolling elements, such as balls or rollers, to reduce friction and improve the wear resistance of the sliding surface. This design typically has a higher load carrying capacity and a lower coefficient of friction, making it suitable for applications that need to withstand large workpieces or high cutting forces.
3. Linear guide rail: Linear guide rail adopts the linear motion design of slide block and guide rail. It typically uses balls or rollers to provide smooth linear motion. Linear guides are suitable for applications that require precise movement in one direction, such as CNC machine tools.
4. Air-floating guide rails: Air-floating guide rails use gas (usually air) to form a thin film, allowing the workbench or slider to almost float on the base. This design can reduce friction and improve the smoothness of motion, and is suitable for high-precision processing that is sensitive to friction.
5. Hydraulic Guides: Hydraulic guides use liquid-filled hydraulic cylinders or plungers to provide smooth movement. This design is often used in large machine tools and can provide higher load capacity and higher rigidity.
Each smoothing form has its advantages and disadvantages, and selecting the appropriate form depends on specific application needs, load requirements, and requirements for accuracy and stability. In practical applications, different vertical lathe manufacturers may adopt different chassis smooth forms to meet customer needs and provide specific performance characteristics.