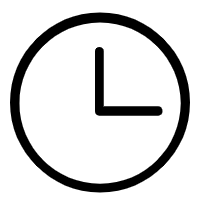
Power supply failure analysis for CNC vertical lathes is a multi-faceted process that requires detailed inspection and diagnosis of the power supply system and its associated components. Here are some possible power failure analysis steps and considerations:
1.Visual inspection method:
Visually check whether the power plug of the CNC vertical lathe is loose, the power cord is broken, or there is other physical damage.
Observe whether the power switch of the CNC vertical lathe is working properly and whether there are any abnormal sounds or smells.
Check the CNC vertical lathe power socket and distribution box to ensure they are in normal condition and supply stable power.
2. Instrument inspection method:
Use a tool such as a multimeter to measure the voltage and current of the power cord to confirm that they are within the normal range.
Test the AC and DC power supply voltages of each group to find possible fault points.
Use an oscilloscope to observe the amplitude, phase, etc. of the power-related pulsation signals to determine the stability of the power supply.
3. Power supply output voltage accuracy:
The regulated DC voltage at each level of the CNC system should be kept within ±5% of the rated value. If it exceeds this range, the voltage adjustment potentiometer should be adjusted to the standard value.
If the voltage of the CNC vertical lathe cannot be adjusted to the standard value, the potentiometer or voltage regulator tube may be damaged and needs to be replaced.
If the voltage of only one gear deviates greatly, the rectifier diode of that gear may be damaged and the diode of the same type needs to be replaced.
4. Special sound analysis:
If the CNC vertical lathe power supply makes repeated special sounds, it may be caused by the operating frequency being too low. At this time, you can use an oscilloscope to test the pulse width modulator to see if it is working properly.
If the capacity of the timing loop capacitor becomes larger, it may also cause the oscillation frequency to be too low, and a suitable capacitor needs to be replaced.
5. CNC vertical lathe signal and alarm indication analysis method:
Analyze CNC vertical lathe hardware alarm indicators, including status and fault indicators on various electronic and electrical devices including CNC systems and servo systems.
Check the CNC vertical lathe software alarm indication, such as the fault alarm display in the system software, PLC program and processing program, and determine the possible cause of the fault according to the alarm number and the diagnostic instruction manual.
6. Interface status checking method:
Since modern CNC systems often integrate PLCs, CNC and PLC communicate with each other through a series of interface signals, so checking the status and signal transmission of these interfaces is also part of power failure analysis.
7. Load capacity check:
If the load capacity of the CNC vertical lathe switching power supply is poor, it may also cause the output voltage to decrease. This may be due to the circuit operating point deviating from the linear region, such as the gain of the amplification link being reduced or the detection circuit being in a nonlinear state.
In summary, the power failure analysis of CNC vertical lathes requires comprehensive consideration of multiple aspects, from visual inspection to instrument measurement, to signal and alarm indication analysis, which may be key steps in determining the cause of the failure. When performing fault analysis, you should remain careful and patient to ensure that you can troubleshoot step by step and find the exact fault point. At the same time, in order to ensure the safety and effectiveness of operation, it is recommended to conduct fault analysis and repair work under the guidance of experienced technical personnel.