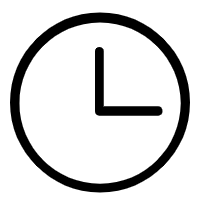
The machining sequence of CNC lathes is a key link to ensure that the machining process is efficient, accurate and safe. The following is a general analysis of the CNC lathe processing sequence:
1. Drawing analysis and process determination:
First of all, the CNC lathe drawings must be interpreted in detail to clarify the size, shape, material and other technical requirements of the workpiece.
CNC lathes determine appropriate processing methods and processes based on drawing requirements and workpiece characteristics, including cutting parameters, tool selection, etc.
2. Preparation of machine tools, cutting tools and fixtures:
According to the process requirements, select the appropriate CNC lathe and install the required tools and fixtures.
Ensure the sharpness and precision of the tool, the stability and positioning accuracy of the fixture.
3. Programming and program verification:
Write CNC programs according to the determined processing technology. This can be programmed manually or automatically using CAM software.
After the CNC lathe is programmed, the program is verified to ensure that the program is correct and can correctly perform the required processing operations.
4. Workpiece installation and tool setting:
Install the CNC lathe workpiece on the CNC lathe to ensure accurate positioning and stable clamping of the workpiece.
The CNC lathe performs tool setting operations to accurately match the relative position between the tool and the workpiece.
5. Rough machining and semi-finishing:
The CNC lathe first performs rough machining to remove most of the remainder of the workpiece, laying the foundation for subsequent processing.
Semi-finishing is then performed to further adjust the shape and size of the workpiece in preparation for finishing.
6. Finishing and fine processing:
CNC lathes perform finishing machining on the basis of rough machining and semi-finishing machining to ensure that the dimensional accuracy and surface quality of the workpiece meet the requirements.
If necessary, fine machining can be performed to further improve the accuracy and surface quality of the workpiece.
7. Inspection and adjustment:
During the processing of CNC lathes, workpieces are regularly inspected to ensure that the processing quality meets the requirements of the drawings.
If substandard products are found, processing parameters or procedures will be adjusted promptly to ensure subsequent processing quality.
8. Disassembly and cleaning:
After the CNC lathe processing is completed, disassemble the workpiece and clean the machine tool and cutting tools.
Perform routine maintenance and upkeep on machine tools to ensure long-term and stable operation of machine tools.
During the entire processing process, you need to pay attention to the following points:
1. Follow the principle of "first inside, then outside, first rough, then fine" to ensure that the CNC lathe processing sequence is reasonable.
2. Minimize the number of workpiece clamping and tool replacement times, and CNC lathes can improve processing efficiency.
3. Pay attention to safe operations, comply with machine tool operating procedures, and ensure the safety of personnel and equipment.
Through the above analysis, it can be seen that the processing sequence of CNC lathe is a complex and delicate process, which requires comprehensive consideration of multiple factors to ensure processing quality and efficiency. In actual operation, the processing sequence and parameters need to be flexibly adjusted according to specific conditions to meet different processing needs.