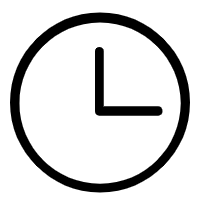
First, the reason of CNC lathe taper analysis
CNC lathe in the process of taper, first need to analyze its reasons. Generally speaking, the reasons for the taper of CNC lathes include the following aspects:
1. Improper tool installation
The motor and servo system of the CNC lathe can accurately control the workpiece speed and the tool movement, but if the tool installation posture is unstable, it will lead to the tool can not accurately contact the workpiece, resulting in taper. Therefore, it is necessary to ensure the necessary adjustment and alignment of the turning tool before processing.
2. Too much cutting force
When the turning tool is subjected to a large cutting force during the processing, or the contact between the tool and the workpiece is unstable during the turning process, it will also lead to the taper of the turning tool.
3. Uneven tool wear
The uneven tool wear of CNC lathes is also one of the main reasons for the taper. When the tool has been worn to a certain extent during processing, when the wear is uneven, the contact point between the tool and the workpiece will not be unified, resulting in taper.
4. The hardness of the processed material is not uniform
When the hardness of the machining material is not uniform, it will lead to uneven abrasion of the CNC lathe machining tool during the wear process, uneven friction, and eventually cause taper.
Second, the countermeasures of CNC lathe taper
In order to avoid taper problems in CNC lathes, the following corresponding measures need to be taken:
1. Ensure the correct installation of the tool
Before processing, the necessary adjustment and alignment of the turning tool should be carried out to ensure that the contact point of the turning tool and the workpiece is in the same plane.
2. Reduce cutting force
Reducing the cutting force of the tool is a key step to avoid taper. It can be achieved by reducing the contact force between the tool and the workpiece and adjusting the processing fluid.
3. Balance wear and tear
When the tool wear is uneven, the tool should be replaced in time, or the wear balance treatment should be carried out to ensure that the contact point between the tool and the workpiece is uniform.
4. Adjust the processing parameters
When the hardness of the material is not uniform, it is necessary to adjust the machining parameters of the lathe, such as adjusting the feed speed and speed of the turning tool to ensure the quality of the processing.
In CNC lathe machining, the taper problem is more common. In view of the taper problem, it is necessary to analyze the problems in the machining process of CNC lathe and take corresponding countermeasures. By analyzing the specific reasons for the taper problem of CNC lathe, regular overhaul, maintenance and maintenance of lathe equipment can ensure the processing quality, improve the processing efficiency, and reduce waste.