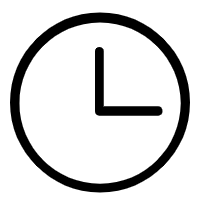
CNC machine tools are important equipment in modern manufacturing. With the development of science and technology and people's increasing requirements for manufacturing accuracy, CNC machine tools are used more and more widely. However, during use, common faults may occur from time to time. This article will introduce common faults and solutions to CNC machine tool processing.
1. The processing accuracy of the machine tool is not enough, and the size of the workpiece does not match the processing program.
At this time, it may be a coordinate error or zero drift during processing. It is necessary to reset the workpiece coordinates and machine tool zero point, and check the lubrication of the machine tool guide rails and bearings and the tightness of the shaft.
2. Harsh noise or vibration occurs when the machine tool is running
It may be that the machine tool bearings are worn or the transmission parts are loose or damaged. The machine tool needs to be fully inspected and the damaged parts must be replaced or tightened in time.
3. The machine tool feed speed is too slow
It may be caused by the failure of the feed servo motor. It is necessary to check the working status of the servo system and replace the faulty parts in time to ensure the normal use of the machine tool.
4. Program execution errors or crashes occur during machine tool processing
At this time, you need to check whether the CNC system and computer settings are correct and whether the program is correct. If necessary, replace the computer or software.
In short, the faults of CNC machine tools are related to their own structural characteristics and usage environment. Therefore, it is necessary to pay attention to care and maintenance during daily use, detect faults in time and carry out repairs to ensure the normal operation and accuracy of the machine tool.