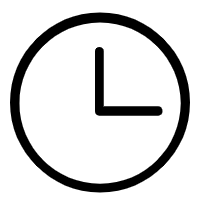
The main function of the CNC lathe lubrication system is to ensure the normal operation of each component of the machine tool, reduce wear, improve machining accuracy and extend service life. Its working principle involves the circulation, distribution and supply of lubricating oil. The specific process is as follows:
After the CNC lathe oil pump is started, it draws lubricating oil from the oil storage tank and pressurizes it through the main pipeline to the quantitative distributor. Each plunger inside the distributor operates sequentially under the pressure of pumping lubricant, distributing lubricant to each oil supply part.
In CNC lathes, after the distributor completes the oil metering and storage action, if the oil pump stops pumping oil, the unloading valve in the pump will enter the pressure relief state. At the same time, the CNC lathe distributor will also act accordingly, pressurizing the lubricating oil measured and stored in the cylinder through the spring that is compressed during oil storage, and then injecting the lubricating oil into the parts that need lubrication through the branch pipe, completing an oil supply action. .
The start and stop time of the CNC lathe lubrication pump, as well as the number and amount of oil supply to the oil supply parts, are controlled by the PLC programming setting of the machine tool. As long as the lubricant entering the progressive distributor maintains a certain pressure, the distributor can work continuously.
During the operation of the CNC lathe lubrication system, if the piston in any intermediate piece is stuck and cannot move, the pistons in other intermediate pieces will all be blocked, and the entire distributor will stop working. At this time, if a proximity switch is installed in the middle piece of the CNC lathe to sense the movement of the piston, it can alarm in time when the piston is blocked, thereby reminding the operator to perform inspection and maintenance.
In addition, different lubrication methods of CNC lathes are also suitable for different processing situations. For example, oil mist lubrication is suitable for high-speed machining and heat treatment processing because it can not only cool the workpiece, but also reduce friction and improve machining accuracy. Oil pump lubrication is more suitable for low-speed processing and heavy-duty processing, because it can greatly reduce wear and friction and extend service life.
In general, the CNC lathe lubrication system ensures that all parts of the machine tool are fully lubricated by accurately controlling the circulation and distribution of lubricating oil, thereby improving processing quality and production efficiency. At the same time, regular inspection and maintenance of the lubrication system are also important measures to ensure the normal operation of machine tools.