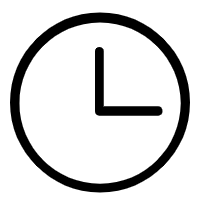
In order to avoid CNC lathe collisions during processing and production, the following measures can be taken:
1. Program verification and simulation:
Before actual production on the CNC lathe, the machining program is verified through CNC lathe simulation software or simulation system. Ensure that the tool path, machining trajectory and motion trajectory in the program are correct to avoid collision between the CNC lathe and the workpiece or fixture.
2. Accuracy of zero point and workpiece coordinates:
Make sure the CNC lathe correctly sets the workpiece coordinates and zero point. Incorrect setting of the zero point of the CNC lathe may cause the tool position to deviate, causing a collision.
3. Setting of safety margin:
Set sufficient safety margins in the CNC lathe processing program to ensure that the CNC lathe tool will not collide with the workpiece or fixture during movement. Reasonable safety margins can prevent potential problems.
4. Use machine parameters:
According to the technical specifications and performance parameters of the CNC lathe, parameters such as the processing speed, feed speed and acceleration of the CNC lathe should be reasonably set. Avoid exceeding the capabilities of the CNC lathe and reduce the risk of machine collision.
5. Tool correction and length compensation:
Regularly perform length correction and radius compensation of CNC lathe tools to ensure that the CNC lathe CNC system has accurate tool size information. This helps avoid collisions caused by incorrectly sized CNC lathe tooling.
6. Monitoring system and alarm settings:
Use the monitoring function provided by the CNC lathe CNC system to set the appropriate alarm threshold for the CNC lathe. Detect abnormal movement of the CNC lathe in time and shut it down to prevent further damage.
7. Personnel training:
Provide professional training to CNC lathe operators to ensure that they understand CNC lathe safety operating procedures, programming specifications and emergency response methods.
8. Regular inspection and maintenance:
Regularly check the mechanical components, sensors, lubrication systems, etc. of the CNC lathe to ensure the normal operation of each component of the CNC lathe. Identify potential problems promptly and perform maintenance.
9.Emergency shutdown device:
Equipped with an emergency stop device for CNC lathes so that the CNC lathes can quickly cut off the power supply when abnormal conditions are discovered to prevent the serious consequences of a machine collision.
10. Use of auxiliary tools:
Use CNC lathe auxiliary tools such as fixtures, sensors, etc. to ensure stable clamping and accurate positioning of CNC lathe workpieces and reduce the possibility of machine collision.
By comprehensively taking these preventive measures, the risk of CNC lathe collisions during processing and production can be effectively reduced, and production efficiency and safety can be improved.