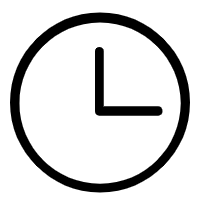
Precision CNC lathes may be affected by a variety of errors during the machining process, and these errors may affect the accuracy of the workpiece. Here are some ways to avoid precision CNC lathe errors:
1. Regular maintenance: Regular maintenance of CNC lathes is the key to maintaining normal operation of machine tools and reducing errors. This includes cleaning, lubrication, and inspection of drivetrains, guide rails, and other components to ensure they remain in good condition.
2. Accurate calibration: Regularly conduct accurate calibration of the CNC system, including encoders, sensors, etc., to ensure the accuracy of system measurement and control.
3. Temperature control: CNC lathes may be affected by temperature changes during processing, and temperature changes may cause expansion or contraction of components such as worktables and guide rails. Using a temperature control system to maintain a stable working environment can help reduce temperature-induced errors.
4. Material selection: When selecting machine tool and workpiece materials, consider their thermal expansion coefficient and other characteristics to reduce errors caused by temperature changes.
5. Tool selection and grinding: CNC lathes use high-quality, high-precision tools, and the tools are ground and replaced regularly. Tool wear will directly affect machining accuracy.
6. Workpiece clamping: CNC lathes adopt a stable and reliable clamping method to ensure that the workpiece will not move or deform during processing. Improper clamping may cause misalignment of the workpiece and affect machining accuracy.
7. Avoid overload: Avoid cutting with excessive load on the machine tool. Overload may cause the machine tool to deform, thereby affecting the machining accuracy.
8. Correct deviations in a timely manner: CNC lathes use feedback systems to detect and correct errors in a timely manner. Through feedback control, the position and speed of the machine tool can be adjusted in time to ensure that the actual processing results are as expected.
9. Reasonable cutting parameters: CNC lathes choose appropriate cutting parameters, including cutting speed, feed speed, etc., to minimize deformation and errors caused by cutting.
10. Employee training: CNC lathe operators are trained to ensure that they use the CNC system correctly and set and adjust machine tool parameters correctly to reduce errors caused by human factors.
By comprehensively considering these factors and taking corresponding measures, errors during precision CNC lathe processing can be effectively avoided or reduced and processing accuracy improved.