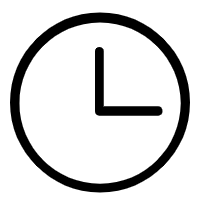
The horizontal machining center (HMC) is a highly efficient machine tool that is widely used in manufacturing. The precise positioning of the cutting tool is crucial for the successful operation of the HMC. Therefore, it is essential to establish a correct coordinate system to perform the machining process.
Coordinate System Calculation
The first step in establishing the coordinate system is to identify the workpiece reference points. These reference points are used to establish the part coordinate system. The reference points are usually located at the corners and edges of the workpiece, and they are used to calculate the X, Y, and Z-axis coordinate positions.
The second step is to determine the tool center point (TCP). The TCP is the point at which the cutting tool contacts the workpiece. Accurate positioning of the TCP is necessary for efficient and precise machining. The machine operator must correctly measure the distance between the spindle centerline and the cutting tool tip. This distance is known as the tool length offset and is used to determine the position of the TCP.
Once the workpiece reference points and the TCP have been determined, the machine operator can establish the machine coordinate system. The machine coordinate system is established by moving the machine's spindle to a known position relative to the workpiece reference points. The operator then enters the X, Y, and Z-axis positions into the HMC's control system. These positions are used to establish the machine coordinate system.
Finally, the operator must establish the part program coordinate system. The part program coordinate system is the coordinate system used to program the machine. The part program coordinate system is established by defining the part zero point, which is the starting point for the part's machining process. The part zero point is usually located at one of the workpiece reference points. Once the part zero point is established, the operator can program the machining operations.
Establishing a correct coordinate system is essential for the efficient and precise operation of the horizontal machining center. The coordinate system calculation process involves identifying the workpiece reference points, determining the tool center point, establishing the machine coordinate system, and defining the part program coordinate system. By following these steps carefully, the operator can ensure that the machining process is accurate and efficient, resulting in high-quality machined parts.