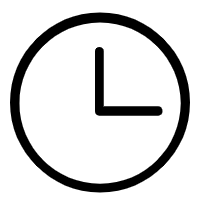
The accuracy inspection of CNC vertical lathes is a complex and important process, involving multiple aspects of inspection. The following are some main inspection steps and methods:
1. Geometric accuracy detection:
Check the flatness of the CNC vertical lathe work surface to ensure that the surface is smooth and has no bulges or depressions.
Check whether the angles generated when the spatial coordinates of the motion axis move in different directions are vertical. This is an important factor in ensuring processing accuracy.
Check whether the central aperture of the CNC vertical lathe spindle and the axis of the rotary axis are perpendicular to the machine tool work surface.
Detect the parallelism of the table when the CNC vertical lathe movement axis moves in the X and Y coordinate directions.
Detect the parallelism of the T-shaped groove side of the moving table in the X coordinate direction.
Detect the straightness of the movement of the CNC vertical lathe headstock along the Z-axis coordinate, etc.
These inspections are usually carried out using tools such as flat rulers and dial indicators to ensure that the geometric accuracy of the CNC vertical lathe reaches the standard.
2. Position accuracy detection:
Positioning accuracy detection: Check whether the CNC machine tool table or other moving parts of the machine tool reach the set motion position during actual operation and whether it is consistent with the programming instructions. This can be done by laser measurement or comparative measurements using a standard scale and optical reading microscope.
Repeated positioning accuracy detection: Measure at the midpoint and any three positions at both ends of each coordinate stroke of the CNC vertical lathe, quickly move and position each position, and repeat the positioning 7 times. The maximum difference in readings is calculated to obtain the repeat positioning accuracy, which is an important indicator for measuring the accuracy and stability of axis motion.
3. Linear motion positioning accuracy detection:
When the CNC lathe and worktable are unloaded, the linear motion positioning accuracy is tested. This is usually done in accordance with national standards and regulations of the International Organization for Standardization (ISO standards), using laser measuring instruments. If a laser interferometer is not used, comparative measurements can also be made using a standard scale and an optical reading microscope.
4. CNC vertical lathe accuracy inspection objects:
Accuracy inspection objects include various components of machine tools, such as gears, positioning holes, support rods, spindles, tool holders, etc. Each part should be carefully inspected and measured to determine the overall accuracy value of the machine tool.
5. CNC vertical lathe accuracy inspection method:
CNC vertical lathe accuracy inspection methods can be divided into automatic inspection methods and manual inspection methods. The CNC vertical lathe automatic detection method is usually programmed according to different models of machine tools, controls the operation of the machine tool, and obtains measurement results from the machine tool. The manual inspection method requires the use of corresponding inspection tools for accuracy inspection.
6. CNC vertical lathe accuracy inspection standards:
CNC vertical lathe accuracy inspection standards are mainly set based on the manufacturing standards of machine tools. Depending on the machine tool manufacturing standards, the corresponding inspection standards are also different. Therefore, the error values between the two need to be controlled within a certain range. For example, for rotational speed error, the standard is generally 1-1.5%, while radial offset error can reach 0.02mm.
Please note that the above are just some basic steps and methods for accuracy inspection of CNC vertical lathes. In actual operation, it may also need to be adjusted and optimized based on factors such as specific machine tool models, specifications, and usage environments. At the same time, when conducting accuracy inspection, it should be carried out in strict accordance with relevant national standards and operating procedures to ensure the accuracy and reliability of the inspection results.