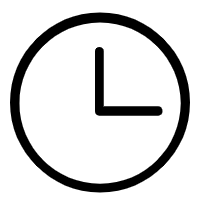
As a highly flexible and automated machining equipment, CNC lathes have a variety of working methods and can adapt to various complex part machining needs. The following are several common working methods of CNC lathes, each tailored to specific machining scenarios, demonstrating the efficiency and precision of CNC technology.
1. Turning processing
This is the most basic working method of CNC lathes, including outer circle turning, inner hole turning, end face turning, etc. By controlling the precise movement of the tool along the X and Z axes, excess material can be cut off on cylindrical, conical, and other workpieces to form the desired shape and size. The CNC system can handle complex contour machining, such as threads, grooves, conical surfaces, etc., while maintaining high precision and repeatability.
2. Boring and drilling
Using specially designed boring cutters or drills, CNC lathes can perform hole machining tasks, including linear boring, step holes, blind holes, etc. By adjusting the feed rate and speed of the tool, it is possible to improve machining efficiency while ensuring aperture accuracy. For deep hole machining, special chip removal techniques and coolant strategies may also be used to ensure machining quality.
3. Cutting and slotting
When it is necessary to separate the workpiece from the raw material or machine grooves on the surface of the workpiece, a CNC lathe can perform cutting and slotting operations. This requires the machine tool to have sufficient rigidity and power, as well as precise tool control, to prevent workpiece deformation or burrs.
4. Precision turning and grinding
For parts that require extremely high surface finish and dimensional accuracy, CNC lathes can perform precision turning by using diamond turning tools or superhard alloy cutting tools. Some advanced CNC lathes are also equipped with built-in grinding functions, which can complete turning and grinding in one clamping process, further reducing errors and improving efficiency.
5. Composite processing
Modern CNC lathes often integrate multiple functions such as milling, drilling, tapping, etc., achieving multi function composite machining with one machine. By equipping milling cutters, drills, taps, etc. with power turrets, other forms of machining can be carried out while turning, reducing the number of clamping times for parts, improving machining accuracy and production efficiency.
6. Automated processing
By equipped with automatic loading and unloading systems, robot arms, or tray exchange devices, CNC lathes can achieve unmanned automated processing. This not only improves production efficiency, but also reduces errors caused by manual intervention, making it particularly suitable for large-scale production environments.
7. Multi axis machining
In addition to traditional three-axis (X, Y, Z) machining, high-end CNC lathes also support linkage machining of four, five, and even more axes, which can handle more complex three-dimensional curved parts, such as turbine blades in the aerospace industry and engine cylinder blocks in the automotive industry. Multi axis machining greatly expands the application range of CNC lathes, improving machining freedom and flexibility.