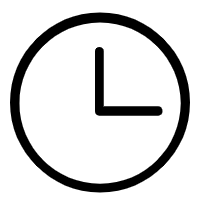
CNC vertical lathes and vertical machining centers, as two important equipment in the field of modern mechanical processing, each have unique advantages and applicable scenarios. They have significant differences in structural design, processing capabilities, and scope of application. Here are the main differences between these two devices to help you better understand and distinguish them.
Structure and Layout
CNC vertical lathe: Its core feature is that the spindle is perpendicular to the ground, and the workpiece is fixed and rotated around the vertical axis for processing. This layout is particularly suitable for processing rotating parts with larger diameters and longer lengths, such as shaft and disc parts. CNC vertical lathes are usually equipped with powerful cutting capabilities and high rigidity structures, capable of efficient turning, drilling, reaming, and threading. Its workbench is usually relatively simple and may not have complex indexing or rotation functions, but it can withstand large workpiece weights.
Vertical machining center: In contrast, the spindle of a vertical machining center is also perpendicular to the workbench, but its design focus is on providing comprehensive three-dimensional machining capabilities. It can not only perform milling, drilling, tapping and other operations, but is usually equipped with an automatic tool changing device (tool library), which can quickly replace different tools to meet the complex machining needs of parts. The worktable of a vertical machining center often has multiple axial degrees of freedom of movement, such as the X, Y, Z axis, and sometimes even a rotation axis, to achieve multi sided machining. This type of equipment is more suitable for processing boxes, plates, molds, and parts with complex geometric shapes.
Processing scope and application
CNC vertical lathe: Due to its design specifically for machining rotating parts, it performs excellently in precision machining of cylindrical, conical, and end faces. Suitable for efficient production of large components in industries such as automobiles, aerospace, energy, and heavy machinery, such as engine crankshafts, gears, bearing rings, etc.
Vertical machining center: It is more flexible in non rotating parts and situations that require integrated processing of multiple processes. It can handle complex 2D and 3D contours, perform various operations such as drilling, tapping, milling, etc., without the need to re clamp the workpiece. Suitable for the production of precision parts, molds, and complex structural components, widely used in precision machinery, electronics, medical devices, and other fields.
Production efficiency and cost
CNC vertical lathe: Due to its specialized processing characteristics, it has extremely high processing efficiency for specific types of parts, especially in mass production. But its processing flexibility is relatively low, which is not suitable for changing processing needs.
Vertical machining center: Although the initial investment cost and maintenance cost are usually higher than CNC lathes, its machining flexibility and automation level are high, which can reduce manual intervention, improve the efficiency of single or multi variety small batch production, and help reduce comprehensive costs in the long run.