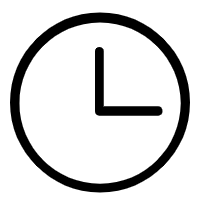
The main reasons for CNC lathe collisions can be summarized as the following points:
1.Program error:
Incorrect CNC programs for CNC lathes are a common cause of collisions. There may be syntax errors, coordinate errors, tool path errors, etc. during the programming process. Program errors can cause the tool to move to inappropriate positions and collide with the workpiece or fixture.
2. Zero point setting error:
If the workpiece coordinate system or tool coordinate system of the CNC lathe is set incorrectly, the reference position of the tool motion will be incorrect, which may cause a collision. Correct zero point setting is critical to ensure correct program execution.
3. Workpiece clamping problem:
Improper workpiece holding on a CNC lathe can cause the workpiece to move or rotate during machining, causing it to collide with the tool. Clamps that are too loose or clamps that are poorly designed can be the cause of the problem.
4. Tool selection and length issues:
Collisions can result from using inappropriate tools or setting the wrong tool length on a CNC lathe. Especially when machining complex workpiece shapes or details, tool selection and length must be carefully considered.
5. CNC system failure:
Hardware or software failures in the CNC system may cause control signal errors, causing the machine tool to be unable to execute instructions correctly, causing a collision.
6. Movement axis failure:
Failures of the CNC lathe's motion axis, such as axis jamming, transmission system failure, etc., may cause the tool position to be inconsistent with expectations, causing collisions.
7. Operator error:
Improper operation by CNC lathe operators, such as not checking the program before starting it, ignoring warning messages, operating errors, etc., are all potential causes of collisions.
8. Initial position setting problem:
Before the CNC lathe starts executing the program, the machine tool needs to correctly set the initial position. If the initial position is set incorrectly, the tool may start moving from the wrong position, causing a collision.
9. Improper maintenance of machine tools:
Lack of regular machine tool maintenance on CNC lathes can lead to component wear or failure, which can lead to collisions.
Understanding these potential causes can help develop effective preventive measures, including regular maintenance, correct programming and operational training.