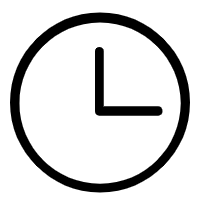
In the manufacturing industry, CNC machining has become an indispensable process. One of the most versatile CNC machining techniques is CNC turning and milling, also known as CNC lathe and mill.
CNC turning and milling is the combination of two processes, CNC milling and CNC turning, in a single machine setup. CNC milling allows for the cutting of complex shapes and forms by utilizing a rotating cutting tool that moves in multiple axes. On the other hand, CNC turning involves the rotation of a workpiece while a cutting tool removes material to achieve a desired shape.
The combination of these two processes in CNC turning and milling allows for a more efficient and accurate machining process. CNC turning and milling is commonly used for the production of complex and precision parts for the aerospace, automotive, and medical industries.
The construction of a CNC turning and milling machine is no simple feat. The machine typically consists of a spindle, chuck, tool turret, and a bed that holds the workpiece. The spindle and chuck are responsible for rotating the workpiece and holding it in place during the machining process. The tool turret holds multiple cutting tools that can be automatically changed during machining.
The bed of the machine is typically made of a heavy-duty material such as cast iron or steel to ensure stability during the machining process. The bed may also have a coolant system to prevent overheating and increase the life of the cutting tools.
In addition to the machine itself, CNC turning and milling also requires specialized software to program the machine. The software allows for the creation of 3D models and toolpaths to guide the cutting tools during machining.
Overall, CNC turning and milling is a powerful manufacturing process that allows for the production of complex and precise parts in an efficient and accurate manner. With the right machine setup and software, it is possible to create a wide range of parts for various industries.