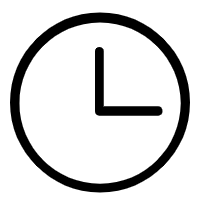
The transmission mode of CNC vertical lathe usually includes spindle transmission and feed shaft transmission. The following are common transmission methods:
1. Spindle transmission:
Direct drive spindle: Some CNC vertical lathes use direct drive spindle, which is directly connected to the spindle through the motor to realize the rotation of the spindle. This method has high rotation speed, fast response and low transmission loss.
Belt-driven spindle: Many CNC vertical lathes use belt-driven spindles. This transmission method transmits power through the belt or chain on the main shaft, and transmits the rotation speed of the motor to the main shaft to realize the rotation of the main shaft.
2. Feed shaft transmission:
Worm gear transmission: The feed axis of CNC vertical lathes often uses a worm gear transmission mechanism, and the transmission is achieved through the meshing of the worm and the worm gear. Worm gear transmission has compactness, precision and high transmission ratio, and is suitable for situations requiring large feed force and torque.
Gear transmission: Some CNC vertical lathes use gear transmission to transmit power through gears to realize the movement of the feed axis. Gear transmission enables larger transmission ratios and higher precision.
In addition, the transmission system may also include other components such as servo motors, gearboxes, and gear grinding transmissions. The specific transmission method will vary according to the design and specifications of the CNC vertical lathe. Different transmission methods have different characteristics and advantages, and can meet different processing needs and accuracy requirements.
It should be noted that the transmission system plays an important role in the CNC vertical lathe, so it needs to be maintained and maintained regularly to ensure the normal operation and life of the transmission components to ensure the stability and processing accuracy of the CNC vertical lathe.