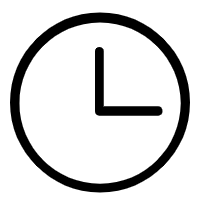
The following three main methods are usually used to process the inner hole surface on a CNC lathe:
1. Drilling: Drilling is one of the most common methods of processing the inner hole surface. On a CNC lathe, a drill bit can be used for drilling operations. The drill bit rotates at high speed and advances in the axial direction to form a hole in the workpiece. This method is suitable for processing inner holes with smaller diameters and shallower depths, and has the advantages of fast processing speed and low cost.
2. Reaming: Reaming is a processing method used to improve the accuracy and surface quality of holes. On a CNC lathe, a reamer can be used for reaming operations. The reamer has multiple edges that allow the hole diameter and surface roughness to be controlled through rotation and axial feed. Reaming is often used to finish holes that have been drilled or roughed to improve dimensional accuracy and surface quality.
3. Boring: Boring is a method used to process large-diameter, long-depth inner holes. On CNC lathes, boring tools can be used for boring operations. The boring tool cuts inside the workpiece through rotation and axial feed, allowing the diameter and shape of the hole to be controlled. Boring can achieve higher machining accuracy and surface quality, and is suitable for inner hole processing that requires higher precision and surface finish.
These three methods can be automated through pre-programmed processing programs on CNC lathes, improving processing efficiency and consistency. Choosing the appropriate processing method depends on factors such as the size, shape, accuracy requirements, and processing efficiency of the inner hole.