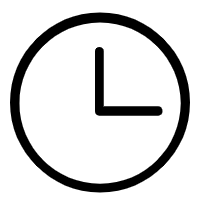
CNC lathe collision is a serious problem that can cause damage to the machine tool and workpiece. Here are some common reasons that can cause CNC lathe collisions:
1. Program errors: When writing CNC programs, if errors occur, such as coordinate calculation errors, tool path planning errors, etc., it may cause the tool to collide with the workpiece or fixture.
2. Zero offset error: If the working coordinate system of the CNC lathe does not match the working coordinate system of the program, or the zero offset setting is incorrect, it may lead to an error in calculating the tool position, resulting in a collision.
3. Tool length compensation error: If the tool length compensation setting of the CNC lathe is inaccurate, the actual position of the tool is inconsistent with the position in the program, which may lead to collision.
4. Wrong tool selection: Using tools that are too long or selecting inappropriate tools may cause collisions, especially in the processing of complex workpiece shapes.
5. Machine tool calibration issues: Errors or wear of machine tool tracks, guide rails, screws and other components, if not calibrated in time, may cause tool position deviations and cause collisions.
6. Workpiece clamping problem: If the workpiece clamping is not firm or the fixture design is unreasonable, it may cause the workpiece to vibrate and move during the processing, and eventually cause a collision.
7. Wrong cutting parameters: Wrong cutting speed, feed speed or cutting depth settings may lead to excessive cutting, causing vibration and collision.
8. Emergency stop and restart: Emergency stop and immediate restart while the CNC lathe is running may lead to inaccurate calculation of tool position and workpiece position, resulting in collision.
9. Human operating errors: CNC lathe operators’ errors in equipment operation, such as incorrect manual operations, accidentally touching the touch screen, etc., may also lead to collisions.
10. Machine tool motion interference: In the complex multi-axis motion of CNC lathes, unreasonable axis motion design or improper program planning may cause interference between machine tool motions, thereby causing collisions.
To prevent collisions, operators should carefully check the CNC program to ensure that the coordinate system and tool parameters are set correctly. In addition, regular maintenance and calibration of machine tools are also important measures to avoid collisions. In operation, careful operation, regular inspection and timely repair of potential problems are effective means to prevent collisions.