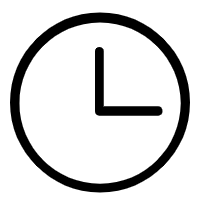
CNC vertical turning and CNC turn-milling are two different types of CNC machine tools. They have some differences in structure, function and application. The following are the main differences between them:
1. Structural difference: The spindle and workbench of a CNC vertical lathe are perpendicular to the ground, and the cutting process is carried out in the vertical direction; while CNC turning and milling compound machine tools usually adopt a horizontal structure, the spindle is parallel to the workbench, and the cutting process is carried out in the horizontal direction.
2. Difference in cutting capabilities: CNC vertical lathes are mainly used for rotary cutting operations such as turning, boring, drilling, etc., and are suitable for cutting axially symmetric workpieces; while CNC turning and milling compound machine tools can not only perform turning operations, but also have Milling function, capable of performing various cutting operations such as plane milling and contour milling.
3. Differences in application fields: CNC vertical lathes are mainly suitable for large-volume, high-precision axially symmetrical parts processing on automated production lines, such as automobile engine crankshafts, transmission gears, etc.; while CNC turning and milling compound machine tools are suitable for a wider range of workpiece processing. Including processing of flat, curved and complex-shaped parts, such as molds, aerospace parts, etc.
4. Differences in control systems: CNC vertical lathes and CNC turn-milling compound machine tools both use CNC systems for motion control and processing program programming. However, because CNC turn-mill machine tools have more cutting methods and axes, their CNC systems are usually more complex, including more coordinate axes and processing control options.
It should be noted that the configuration and performance of specific CNC vertical lathes and CNC turn-mill machines may vary, depending on the manufacturer and model. Therefore, when choosing a suitable machine tool, you need to evaluate it based on factors such as specific processing requirements, workpiece characteristics, and budget, and conduct detailed communication and consultation with the manufacturer or supplier to determine the model and configuration that best suits your needs. .