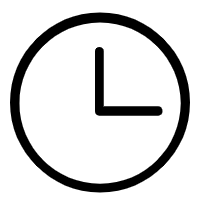
The main reasons for reducing the error of CNC machine tools include the following:
1. Machine tool quality: Selecting high-quality CNC machine tools is the basis for reducing errors. Excellent machine tool design and manufacture can provide higher rigidity, stability and precision, and reduce errors caused by the machine tool itself.
2. Processing technology optimization: Reasonable processing technology design can minimize errors. Including selecting the appropriate tool, cutting parameters, cutting path and feed rate, etc., to ensure a stable cutting process and accurate machining results.
3. Tool selection and management: Selecting reliable tools, such as high-precision tools and tool holding devices, can reduce errors caused by the tool itself. In addition, tools are regularly inspected, replaced and maintained to ensure their good condition and dimensional accuracy.
4. Machine tool debugging and calibration: After the machine tool is installed, accurate debugging and calibration is the key. Including adjusting and calibrating the cutting axis of the tool, the transmission system of the machine tool, and the measuring device to ensure that it meets the design requirements and accuracy standards.
5. Temperature and humidity control: Controlling the ambient temperature and humidity is very important to reduce the error of CNC machine tools. Temperatures that are too high or too low can cause thermal expansion or contraction of machine tool components, causing errors. Excessive humidity can lead to corrosion and wear of machine tool metal parts.
6. Programming and parameter setting: Correct NC programming and parameter setting are essential to reduce errors. Programming should be based on the actual situation to choose a reasonable cutting path, feed rate, tool radius compensation and other parameters. At the same time, proper workholding and machining sequences need to be taken into consideration.
7. Regular maintenance and maintenance: Regular maintenance and maintenance of CNC machine tools, including inspection and maintenance of lubrication systems, guide rails, transmissions, etc. Ensure that the various functions and components of the machine tool are in good condition, and reduce errors caused by wear or looseness.
8. Detection and feedback control: Implementing appropriate error detection and feedback control can correct errors in time and improve machining accuracy. Use high-precision measuring equipment to detect the processing results, and adjust the processing parameters and compensate errors in time.
To sum up, reducing the error of CNC machine tools requires comprehensive consideration of the quality of the machine tool itself, processing technology, tool management, debugging and calibration, environmental control, programming parameters, regular maintenance, testing and feedback control and other factors. Through comprehensive management and optimization, errors can be effectively reduced and the machining accuracy of CNC machine tools can be improved.