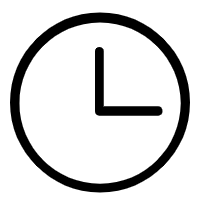
Tool compensation of CNC lathes is a special function used to achieve more precise machining results in turning. During the machining process, due to factors such as the irregular shape of the workpiece or tool wear, the distance between the tool and the workpiece may deviate, resulting in reduced machining accuracy or unstable machining quality. The tool compensation function can solve this problem by adjusting the distance between the tool and the workpiece in real time, thereby achieving more accurate processing results.
There are many specific ways to implement tool compensation, but the basic principle is to achieve the purpose of reducing machining errors by adjusting the coordinate axis or radius parameters of the tool. Different CNC lathe manufacturers may use different compensation methods and algorithms, and provide corresponding adjustment parameters for operators to use. In the actual processing process, appropriate adjustments need to be made according to the shape and size of the specific workpiece, the use of the tool and other factors to ensure the stability and accuracy of the processing effect.
Generally speaking, tool compensation is an important technical function on CNC lathes. It can effectively improve processing efficiency and processing quality, reduce scrap and defective product rates, and provide strong support for the company's production costs and competitiveness. Therefore, for companies that require fine machining and high-precision machining, choosing a CNC lathe with tool compensation function will be a very necessary and beneficial choice.