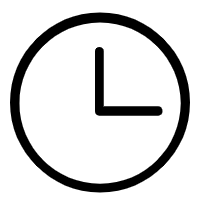
Automobile brake disc production line usually requires the following equipment and processes:
1. Cutting equipment: used to cut raw materials (usually iron plates) into brake disc precursors of suitable size. Common cutting equipment includes CNC cutting machines, shears, etc.
2. Lathe: used for precision machining of brake discs, including turning, drilling and chamfering. CNC lathes offer greater precision and automation.
3. Grinding machine: used for surface grinding, chamfering and polishing of brake discs to provide better surface quality and braking performance.
4. Stamping equipment: used to punch out special shapes such as mounting holes, heat dissipation holes and weight-reducing holes on the brake disc.
5. Welding equipment: Some brake discs require welding to secure additional structural parts or connectors.
6. Heat treatment equipment: Some brake discs require heat treatment, such as quenching and tempering, to improve strength and hardness.
7. Spraying equipment: used to coat or rust-proof brake discs to improve corrosion resistance.
8. Quality inspection equipment: including physical performance testing instruments, geometric measuring equipment, etc., used to detect and ensure the quality of brake discs and compliance with required specifications.
In addition, the production line also requires conveyor systems, clamping devices, control systems and automation equipment to automate the production process and improve production efficiency.
It should be noted that the specific equipment and processes of the brake disc production line may vary according to different production scales, product types and manufacturers' requirements. It is recommended to refer to relevant industry standards and manufacturer recommendations to determine which equipment and processes are suitable for a specific production line.