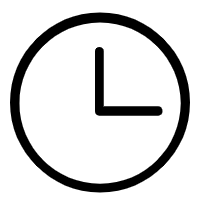
The working efficiency of CNC lathes is affected by many factors. The following are some main factors:
1. Tool selection and grinding conditions:
Appropriate tool selection and good grinding conditions for CNC lathes are directly related to processing quality and speed. Worn CNC lathes or improperly selected tools can result in inefficient cuts and increased machining time.
2. Cutting parameter settings:
Proper cutting speed, feed rate, and depth of cut settings on your CNC lathe are critical to maintaining efficient machining. Incorrect parameter settings for CNC lathes may result in premature tool wear, reduced machining quality, or increased machining time.
3.Material properties:
Different materials of CNC lathes have different hardness, toughness and cutting properties. A cutting process that is poorly adapted to CNC lathes may result in low efficiency. CNC lathes Taking into account the characteristics of the material, CNC lathes using appropriate cutting strategies are the key to improving efficiency.
4. Machine tool rigidity and stability:
The rigidity and stability of a CNC lathe are directly related to its performance in high-speed cutting. The low rigidity of CNC lathes may cause vibration and deformation, affecting processing accuracy and efficiency.
5. Automatic tool changing system:
A good automatic tool change system for CNC lathes can reduce tool replacement time and improve production efficiency. On the contrary, unstable or improper operation of the CNC lathe tool changing system may lead to production interruption and reduced efficiency.
6. CNC programming and program optimization:
Efficient CNC programming and program optimization of CNC lathes can minimize non-processing time such as idle time and rapid movement time, and improve the utilization rate of CNC lathes.
7. Coolant system:
The effective coolant system of CNC lathes can keep the tools and workpieces within the appropriate temperature range and prevent overheating. CNC lathes improve cutting efficiency and tool life.
8. Operator skills and training:
The skill level and training level of CNC lathe operators have a direct impact on the work efficiency of CNC lathes. Skilled operators of CNC lathes can set up the machine faster, adjust parameters, and respond to problems in a timely manner.
9. Equipment maintenance and upkeep:
Regular equipment maintenance and upkeep of CNC lathes can ensure the normal operation of CNC lathes, reduce CNC lathe failures and production interruptions, and improve work efficiency.
10. Workpiece clamping method:
Effective workpiece clamping methods on CNC lathes are crucial to ensuring the stability and accuracy of the workpiece. Poor clamping on a CNC lathe can cause processing interruptions and quality issues.
11. Tool path planning:
CNC lathes can reasonably plan tool paths to reduce idling and rapid movement, and CNC lathes can effectively improve processing efficiency.
Taking these factors into consideration, the working efficiency of CNC lathes can be optimized and productivity and processing quality improved.