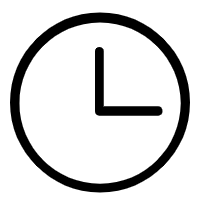
There are many possible reasons why the CNC vertical lathe may vibrate when it moves quickly. Here are some common causes:
1. Mechanical looseness: During rapid movement, if the parts, fixtures or connections of the machine tool are loose, it will cause the machine tool to move in vibration. This may be caused by prolonged use or improper maintenance.
2. Insufficient rigidity: Insufficient rigidity of the machine tool means that the machine tool cannot effectively resist the vibration effects of cutting forces and inertial forces when moving rapidly. Insufficient rigidity may be caused by unreasonable design, insufficient material strength or aging of machine tools.
3. Cantilever effect: For vertical lathes, the workpiece is fixed on the spindle and is far away from the machine tool structure, which may cause a cantilever effect. The cantilever effect causes increased vibration and jitter when moving quickly.
4. Imbalance: If the machine tool spindle or tool system is unbalanced, it will cause vibration and jitter during rapid movement. This may be caused by factors such as uneven cutting tool wear or poor spindle dynamic balance.
5. CNC system problems: The CNC system's inability to accurately control the position and speed of the processing axis during rapid movement may also cause vibration and jitter. This may be due to issues with the control algorithm, feedback sensors, or system settings.
In order to solve the jitter problem when CNC vertical lathes move quickly, the following measures can be taken:
6. Regularly check and tighten all parts of the machine tool to make sure there is no looseness.
7. Perform necessary maintenance and maintenance according to the machine tool manufacturer's recommendations to maintain the rigidity and stability of the machine tool.
8. Reasonable selection of cutting parameters, including cutting speed, feed rate and cutting depth, to reduce vibration and jitter.
9. For the problem of cantilever effect, the clamping position of the workpiece can be adjusted appropriately to reduce the length of the cantilever.
10. Adjust the balance of the tool system to ensure the dynamic balance of the cutting tool and the spindle.
11. Check the settings and parameters of the CNC system to ensure its normal operation and precise control of the position and speed of the machining axis.
It is necessary to conduct comprehensive analysis and judgment according to the specific situation and the characteristics of the machine tool, and sometimes professional maintenance and debugging may be required to eliminate the vibration problem and improve the stability of the machine tool. It is recommended to consult a professional machine tool manufacturer or maintenance personnel for more detailed technical guidance and support when necessary.