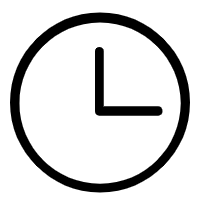
There are several possible reasons why tool vibration (or vibration cutting) may occur when machining die castings on a CNC lathe, including:
1. Unsuitable tools: If the CNC lathe uses tools that are not suitable for processing specific types or characteristics of die casting materials, it may cause tool vibration. For example, if the tool edge design is improper, the tool material is unsuitable, or the tool is severely worn, it may cause vibration during cutting.
2. Incorrect CNC lathe processing parameter settings: If the CNC lathe processing parameter settings are incorrect, such as CNC lathe feed speed, cutting depth, cutting speed and other parameters that are set too high or too low, it may cause tool vibration. Too high cutting parameters of CNC lathes may cause excessive vibration between the tool and the workpiece, while too low cutting parameters may lead to insufficient cutting and unbalanced cutting forces.
3. The workpiece is not clamped firmly: If the CNC lathe's die-casting parts are not clamped firmly during processing, or the clamping device becomes loose or fails, it may cause the workpiece to vibrate during the cutting process.
4. CNC program programming problems: If there are errors in the CNC program programming of the CNC lathe, or the tool path design is unreasonable, it may also cause tool vibration. For example, too rapid tool path turning or excessive changes in the cutting path of a CNC lathe may cause vibration during cutting.
5. Machine tool structural problems: If there are structural problems with the CNC lathe itself, such as insufficient bed rigidity, guide rail wear, spindle axial looseness, etc., it may also cause tool vibration.
To solve the vibration problem of CNC lathes, it is necessary to comprehensively consider the above possible causes and take corresponding measures, such as replacing suitable cutting tools, adjusting processing parameters, checking the workpiece clamping device, optimizing CNC programming, overhauling the machine tool structure, etc.