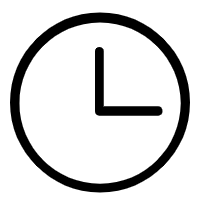
In CNC vertical lathes, correct workpiece positioning and clamping are the keys to ensuring machining accuracy and safety. The following are some important things to note when positioning and clamping the workpiece:
1. Workpiece preparation:
Before machining on a CNC vertical lathe, make sure the surface of the workpiece is clean and free of oil or debris.
Ensure that the size of the CNC vertical lathe workpiece meets the processing requirements and there are no obvious defects.
2. Positioning benchmark:
To determine the exact positioning datum for a CNC vertical lathe workpiece, a specific surface or edge of the workpiece is usually selected.
Use a suitable measuring tool, such as a micrometer or coordinate measuring instrument, to ensure accurate positioning.
3. Fixture selection:
Select appropriate fixtures for CNC vertical lathes and determine the fixture type based on the shape and size of the workpiece.
The fixture should provide sufficient support and stability to prevent the workpiece from moving or vibrating during machining.
4. Clamping force control:
Control the clamping force to ensure that the CNC vertical lathe fixture tightens the workpiece without deforming or damaging the workpiece.
Avoid using excessive clamping force to avoid deformation of the workpiece or internal stress during processing.
5. Symmetrical clamping:
Try to use symmetrical clamping methods to ensure that the CNC vertical lathe workpiece is evenly stressed and avoid tilting or deforming the workpiece due to uneven clamping.
6. Clearance between tool and workpiece:
When clamping the workpiece, sufficient clearance between the CNC vertical lathe tool and the workpiece should be considered to ensure normal movement of the tool and prevent collision.
7. Check the stability of the fixture:
Before processing, carefully check the stability of the CNC vertical lathe fixture to ensure that the fixture is firmly fixed on the machine tool.
8. Reserve margin:
When clamping the workpiece on a CNC vertical lathe, some margin can be reserved to take into account possible processing deformations in order to finally obtain the required dimensions.
9. Regular inspection:
CNC vertical lathes regularly check the status of fixtures and clamping devices to ensure they are working properly and avoid problems caused by wear or failure.
10.Safety considerations:
CNC vertical lathes ensure operator safety when clamping workpieces. Avoid possible dangers caused by sudden loosening of fixtures or workpieces.
The above precautions can help ensure that the CNC vertical lathe can obtain a stable processing process and high-precision processing results when positioning and clamping the workpiece.